Since its introduction in 2007, the Energy Performance Certificate (EPC) has been the main method of assessing the energy efficiency of buildings in the UK. The Government has recently revisited the EPC requirements, seeking to update them and make them more stringent. Currently, proposed Minimum Energy Efficiency Standards (MEES) legislation mandates a phased implementation of the EPC B by 2030 requirement, with EPC C by 2027 set as an interim milestone for all commercial non-domestic buildings.
The new requirements represent a significant challenge for landlords. Over 75% of London office space is presently below EPC B standards[1]. Given the challenges involved, many of our clients are seeking a better understanding of the risks and opportunities they are facing. To that end, we have developed an illustrative case study using our cost information and understanding of the new requirements. In our example, we provide some indicative costs of improvement, along with some commentary on programme implications. We also provide advice on what elements need refurbishing, ranging from more elementary changes to more complicated MEP and system replacements.
We provide detail below, but in summary the new requirements mean that owners may incur significant costs from the proposed changes, depending upon their starting point. Typically, to go from EPC D to C, costs can range from £30-60/sq ft while going from EPC C to B/A can range from £50-75/sq ft. Correspondingly, programmes for this type of work can stretch from 24 weeks to 76 weeks depending on the desired rating and size of the building.
Some background: EPC and proposed changes to MEES
An EPC indicates a building’s energy efficiency by rating it from “A+” (very efficient) to “G” (inefficient). It is very similar to the kind of energy ratings you see for common household appliances.
An EPC certificate must be obtained from an approved commercial energy assessor and is valid for 10 years, after which time it must be renewed. The EPC is a measure of the building’s energy efficiency as it is built (generally speaking, its systems and fabric). The rating is not based on the actual energy consumption of the premises.
It is important to note that an EPC measures efficiency from a design and not operational standpoint. For example, an appliance (or building) could be rated “A” but also run constantly. It would be energy efficient from a design perspective, but still use a lot of energy (and emit a lot of carbon). Conversely, a “D”-rated appliance (or building) that never ran would be inefficient from a design standpoint, but also low energy and carbon. It is therefore important to remember that an EPC is only a measure of design efficiency.
Minimum Energy Efficiency Standards (MEES) originated in the Energy Act 2011, with EPCs as the benchmark for buildings. MEES has been in force since 2018 and to date has required buildings to attain at least an “E” rating before they can be leased or sold. As of April this year, the “E” requirement extends to the continuation of existing leases.
There are some exemptions to this rule, including Listed buildings, instances where improvements would have a very long payback (more than seven years), and so on. But by and large, an EPC is expected of commercial buildings at the time of sale or lease.
The Government is now considering a requirement that all commercial non-domestic buildings achieve an EPC “B” rating by 2030, with an interim rating of “C” required by 2027. In order for this to be possible, many buildings will need to make significant changes, including replacing building systems and fabric.
Not surprisingly, the costs of improving can be significant. At G&T we have reviewed what improvements could be undertaken and what this means in terms of options and expenses. In the example that follows, we show typical interventions and costs involved with meeting the new requirements of MEES regulation.
Case Study
Our case study cost model is based on a typical commercial building located in Central London and built in the late 1980s. It has a current EPC rating of “D.” This exercise provides the estimated cost uplift for upgrading the building elements to improve the EPC rating from a D to an A.
We have assumed the following notional key building metrics for the cost model:
- Eight storeys inclusive of one basement floor for ‘back of house’ spaces such as plant
- Typical floor to floor height of 4m
- Typical floor perimeter of 136m
- Total wall area of 4,350m²
- Solid to glazing ratio of 60:40
- Solid element of external wall has at least 150mm of insulation
- Existing energy source is gas-fired boilers
- Fluorescent luminaires and original fittings dating c. 1980-1990
- Limited lighting control system and BMS
- No photovoltaics or space allocation
- Fully mechanical ventilation system
- Efficient rectangular building
- Typical floor area of 12,500 sq ft
- Total GIA of 100,000 sq ft
- Overall nett: gross of 70% with a typical floor assumed to be 80%
Outline costs
Potential interventions and costs to upgrade this building from its current level to a “C” or “B” rating would be as follows:
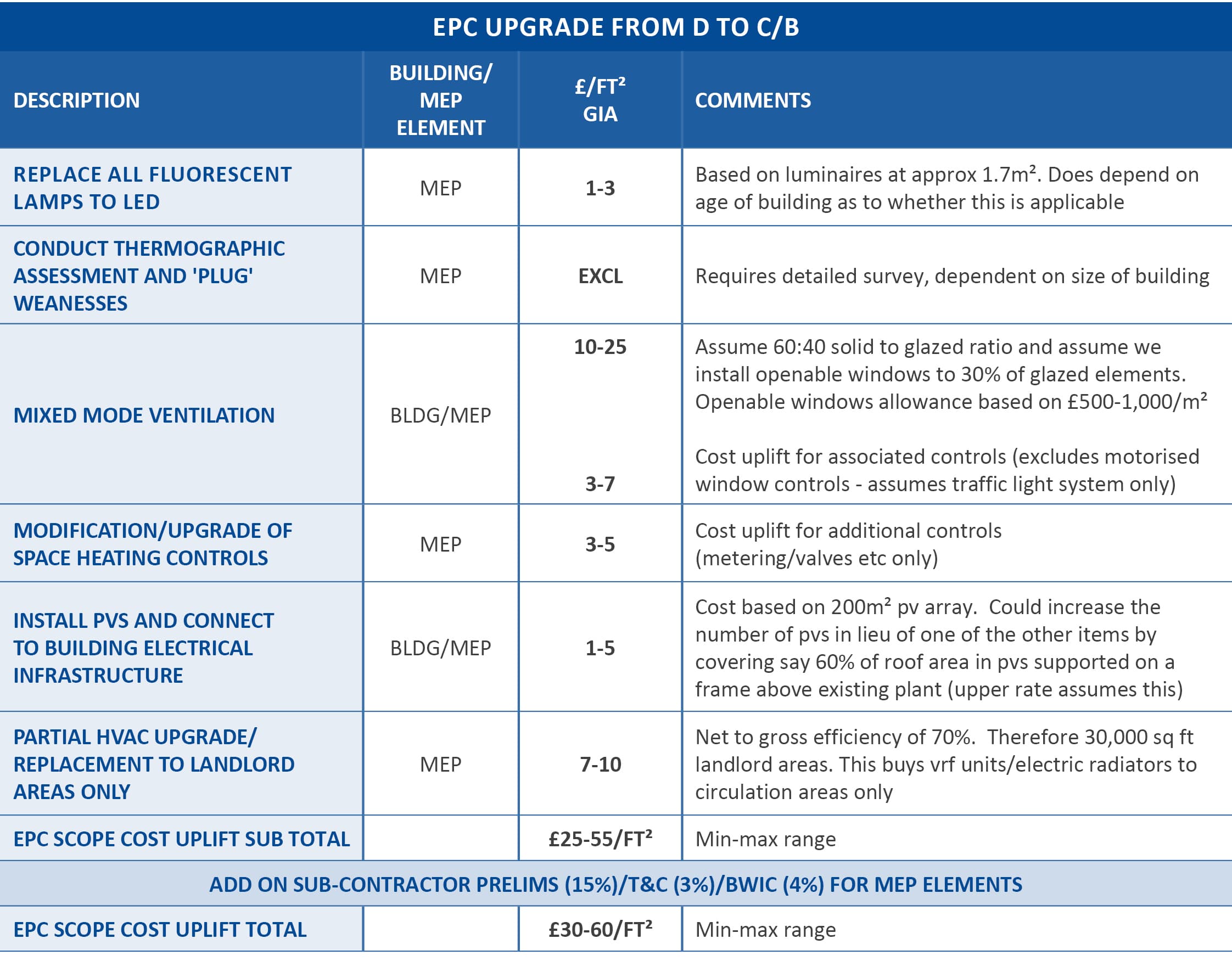
Note: The above costs exclude main contractor on-costs of circa 14%; 6% OH&P and 3% contingency. This list is not exhaustive and is to be used as a guide only. Due to every building being unique, not all the above items may be required to achieve an EPC rating upgrading. Similarly, additional items may be required to achieve the desired EPC rating.
To raise the building from “C” to “B” or an “A” rating would require upgrades such as the following:
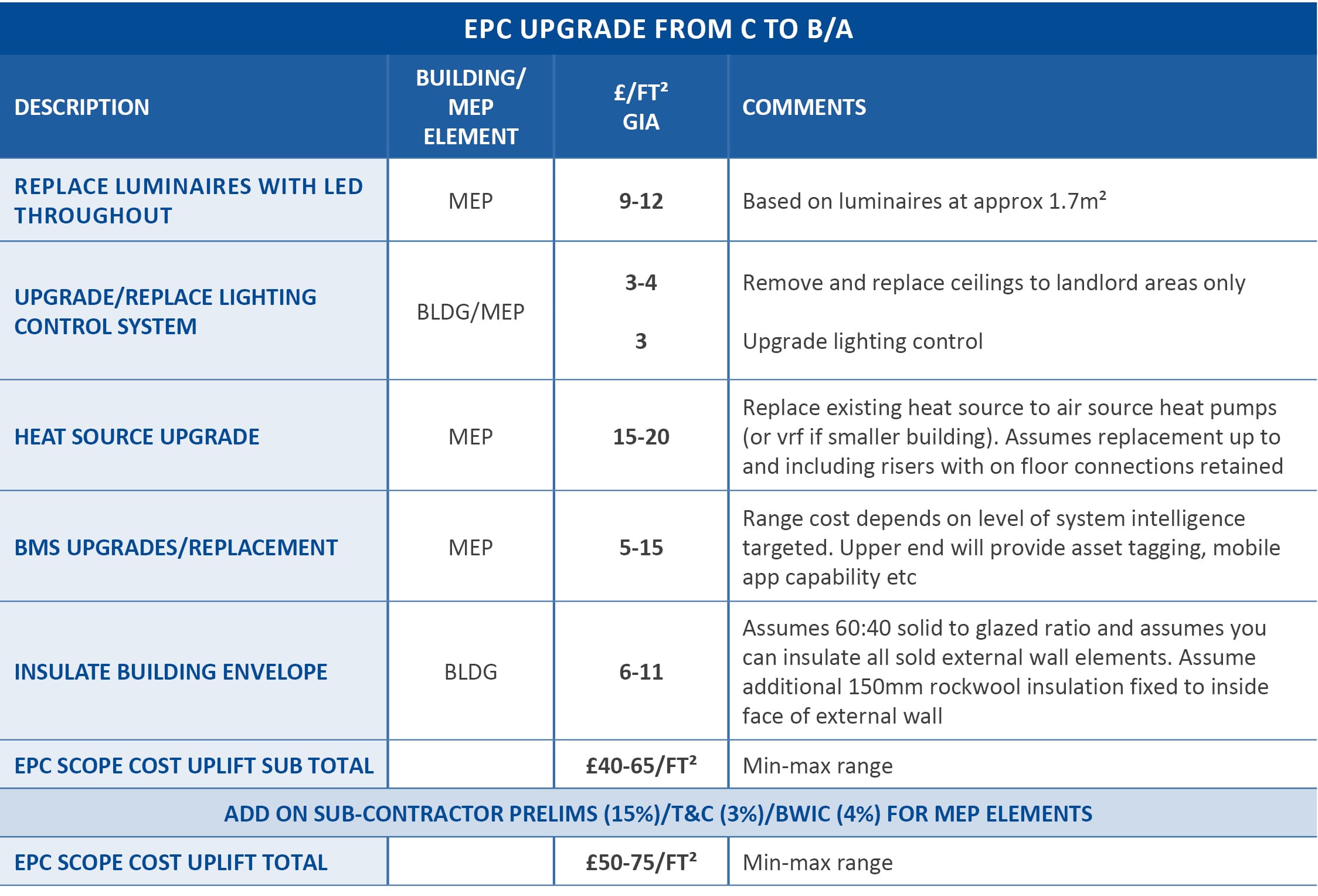
Note: The above costs exclude main contractor on-costs of circa 14%; 6% OH&P and 3% contingency. This list is not exhaustive and is to be used as a guide only. Due to every building being unique, not all the above items may be required to achieve an EPC rating upgrading. Similarly, additional items may be required to achieve the desired EPC rating.
In terms of programme, it is hard to prescribe a likely programme for EPC related work, but it could range from 24 to 76 weeks dependent on the desired scope of the scheme, with long lead MEP equipment and the size of the building determining the length.
Discussion
As the above example makes clear, there are many types of interventions possible. These include upgrades to fixed services, such as lighting, or the introduction of new or improved controls devices. More significant action may be required, including the upgrading of heating systems by replacing gas with all-electric heat pump systems (it may be possible for tenants to remain in place when this occurs). Other improvements to the building fabric can be harder to deliver with tenants in-situ and may better be planned as part of major refurbishment work.
There are real concerns that the repairs needed to improve EPCs are too difficult and costly. That may be one reason why the MEES regulations have not been finalised, even though this was expected long ago. There is also a widespread belief that EPCs are very poor predictors of actual energy used and carbon emissions. It is well known that there is a weak correlation between the EPC rating and actual energy use and carbon emissions. It is not uncommon to have a building with an EPC rating of “A” that uses a large amount of energy, or a building with a lower EPC that is run better, or has fewer loads, and therefore uses less energy.
The ”performance gap” between predicted and actual energy usage is one reason why Government has instituted a competing consultation on performance-based buildings. The consultation paper signalled Government plans to introduce a programme in which a building’s actual performance would be the basis of its energy rating.
At the time of both consultations, it was anticipated that the Government would publish responses in late 2021 concerning MEES improvements. To date no responses have been published, raising doubts about whether it will be realistic to impose an interim milestone of “C” for 2027.
Conclusion
At the moment, the proposed MEES changes have yet to be enacted as part of legislation. But the prudent response is for clients to prepare for and at the very least anticipate the kinds of costs and programme implications that could ensue from Government action. The best and least risky approach is to assume that EPCs will need to be improved at some point and that, above all, energy performance (in terms of consumption) is also a regulatory target here to stay.
Therefore, building owners should aim to get ahead of regulation and budget for plant and fabrics improvements, as these are effective measures for any performance-based ratings that could emerge aside from the EPC rating system. They should also align this programme of work with tenancies or other planned refurbishments, so as not to miss opportunities to enact improvements at the most cost-effective time.
G&T is well placed to assist landlords and occupiers with our recent experience in this type of work on projects of all sizes, with the ability to provide both project and cost management services. If you would like advice on how to upgrade your building’s EPC rating, get in touch with our experts today.