Introduction
The construction industry, long known for its resilience and adaptability, is undergoing a profound transformation thanks to the latest advancements in construction materials technologies. These innovations are not only enhancing the efficiency and sustainability of construction projects but also revolutionising the very foundations of how we build our world. In this article, we'll explore some of the most promising developments in construction materials that are shaping the future of the industry.
Some of the materials mentioned in this article may be considered niche, having previously failed to achieve uptake at scale, but their potential is nonetheless exciting. Furthermore, as the technologies evolve, their use cases broaden and their viability improves, we may see more and more of these technologies being utilised on construction sites across the UK.
G&T has experience in the use of a wide range of alternative materials and methods of construction. We are closely tracking the development of these new technologies and forging strong relationships with the most cutting-edge manufacturers to help keep our clients informed about the emerging opportunities in this field.
Self-healing Concrete
Concrete is the backbone of modern construction. It’s a versatile and widely used material, but it's also susceptible to cracks and damage over time. Enter self-healing concrete, a potentially transformative technology where durability is a concern.
Self-healing technologies may have been around for some time, but technological developments and elevated concrete prices have prompted renewed interest for self-healing concrete, particularly on infrastructure projects, where its use could reduce cement contents.
There are four main different techniques to promote self-healing in concrete:
- Capsules: Tiny capsules containing healing agents are added to concrete mixes. When cracks form, these capsules break, releasing the agents (like sodium silicate) that react with water to seal the cracks. However, once ruptured, the concrete can't self-heal further.
- Bacteria: Special bacteria are mixed into concrete along with nutrients. When cracks appear and water enters, the nutrients dissolve, feeding the bacteria. This prompts them to generate calcium carbonate, which fills the cracks, facilitating self-healing.
- Shape Memory Polymers: Shape memory polymers are integrated into concrete structures. When cracks occur, a heating wire system triggers these polymers to contract, pulling the structure back into its original shape.
- Vascular: Concrete features artificial channels through which healing agents can be pumped as damage occurs. Advanced mini vascular networks, like 3D-printed tetrahedral units, store and release bacterial agents when mechanical stresses reach a certain threshold, sealing cracks in a self-healing process.
Cracks in concrete are a common phenomenon due to its low tensile strength. Cracks impair the durability of the material as they provide an easy path for liquids and gasses to move through. If these cracks grow to reach the reinforcement, the steel bars could corrode. By making sure that the concrete seals up any cracks before water reaches the rebar, the steel is kept safe for longer and prolongs the life of the structure.
Although concrete contains some natural, autogenous healing properties (due to ongoing hydration of clinker minerals or carbonation of calcium hydroxide), this is limited to small cracks and is only effective when water is available. However, modified self-healing concrete provides more control over cracking, not only extending the lifespan of structures but also reducing maintenance costs significantly.
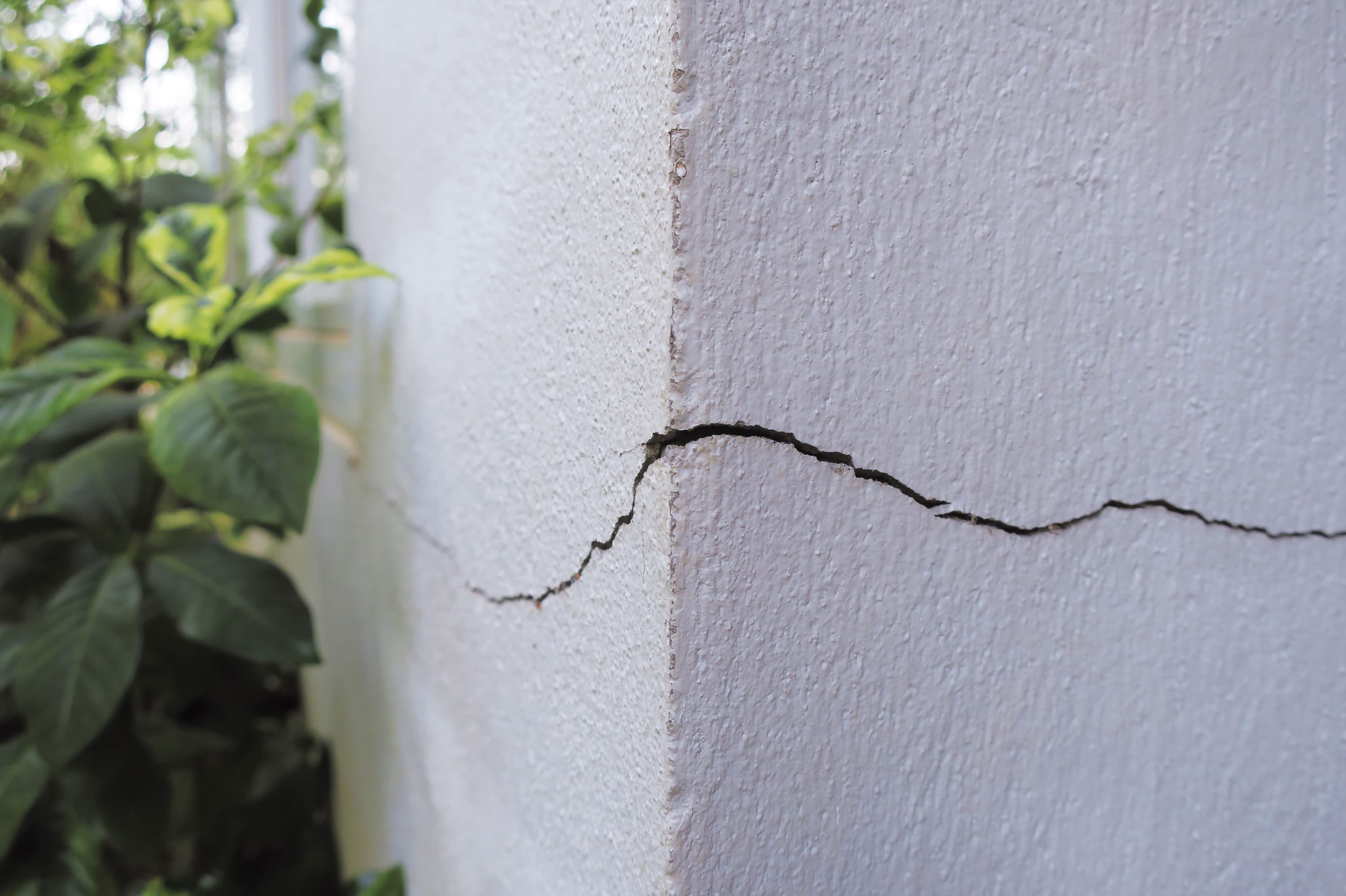
Bacteria-based, Self-Healing Concrete
One of the few companies offering self-healing concrete commercially in the UK is precast specialist JP Concrete. Its self-healing system (called ‘sensicrete’) uses limestone-producing bacteria, which sleep in the concrete until woken by air and water, which get in through cracks. When the bacteria are activated, they start to produce limestone. The limestone fills and seals the crack and the water is driven back. Once the limestone crack is sealed, the bacteria go back to sleep. Products such as sensicrete can therefore make concrete much more durable, extending the life of a structure and reducing its maintenance costs.
Self-healing concrete products will be vital in reducing cement-based CO2 emissions (which are projected to double by 2050 in the UK).[1] Traditionally, repair methods have required more concrete material, adding to the carbon emissions already produced during concrete production. However, self-healing concrete removes the need for additional concrete when repairing concrete structures. In fact, self-healing concretes can capture CO2 directly out of the air in the process. For example, Enzymatic Inc. claims that its enzyme based, biological self-healing concrete uses ambient CO2 in the air (and H20) to produce the calcium carbonate. Its ability to remove CO2 from the air and safely store it as calcium carbonate crystals, in addition to its ability to repair rather than replace concrete, makes the technology green and beneficial to the environment.[2]
This novel approach of developing concrete that can ‘heal’ is all well and good, but unless these technologies can be scaled up, they will bring little benefit to the construction sector.
Suppliers, contractors, and designers all want to build more sustainably and responsibly, but some estimate that the industry could still be a decade away before self-healing concrete is commonly used in commercial applications. Certain hurdles must be overcome before production becomes widespread. The industry will want examples of its successful use across a range of projects, while new standards, guidance and codes of practice will need to be developed to alleviate any potential concerns. Cost is another limiting factor. Costing 10-30% more upfront than traditional concrete[3], self-healing concrete is not currently considered economically viable for normal construction where a high volume of the material is required.[4] In the meantime, its use is likely to be limited to demonstrator projects or mission-critical infrastructure, where the benefits of long-term robustness of the material far outweigh the initial costs.
Reducing the CO2 Content of Cement
As the most frequently used building material and the second most used substance in the world, after water, concrete has a colossal carbon footprint. In fact, about 8% of global emissions caused by humans come from the cement industry alone.[5]
Despite only making up around 10% of concrete by volume, around 75-90% of concrete’s embodied carbon contribution comes from the cement element[6] (where the mix utilises 50% ordinary Portland cement replacement in the form of GGBS).[7] One strategy being considered to reduce emissions from concrete is replacing/substituting the cement with supplementary cementitious materials (or SCMs).
Seratech, a sustainable construction materials business, has developed a process that consumes olivine and waste CO2 from flue gases and produces two products which both have significant value in construction:
- Silica (which can be used as an SCM)
- Magnesium carbonate (used to make a range of zero carbon construction materials and consumer products, including alternatives to building blocks and plasterboard)
The use of silica as an SCM means the amount of Portland cement in the concrete can be cut by up to 40%. However, as the silica comes from a process that captures CO2 it is “carbon negative” and the concrete can become carbon neutral. Nothing else in the concrete needs to be changed.[8]
Furthermore, Seratech’s silica SCM can be used in a variety of applications, with no specialist equipment required or retraining of those workers who pour the cement on site. Its carbon neutral product was showcased as the 2022 London Design Festival, as a bespoke architectural installation engineered by AKT II.[9]
Although the chemistry could be a game-changer, getting architects, designers and contractors to adopt and use the product (and others like it) en masse could be challenging. Demonstrator projects will be required to convince stakeholders that such products are cost-effective, viable and safe.
“While we must strive to increase design efficiency and reduce material demand, we must also urgently reduce the embodied carbon in our building materials. The Seratech process offers the potential to rapidly decarbonise cement production at scale, capturing CO2 while producing useful cement replacement materials for use in concrete, bricks and other construction products. We are working closely with the Seratech team to accelerate the adoption of this exciting technology.”
In the meantime, contractors such as Laing O’Rourke have begun to mandate the switch to low carbon variants of concrete on all its new UK projects (using lower carbon alternatives to Portland cement, such as GGBS and Pulverised Fly Ash[10]). One version, called Cemfree, can save 85% of embedded carbon compared with traditional mixes.[11] However, Laing O’Rourke’s announcement followed a long-term research programme[12] that proved a range of low carbon concrete options can be successfully deployed on projects as a like-for-like substitute for traditional concrete.
At this juncture, it is perhaps worth noting that there are also concerns about the availability of GGBS and its impact on global emissions. A paper published by The Institution of Structural Engineers and others[13]
highlighted that while GGBS is an excellent SCM that can help reduce demand for carbon-intensive Portland cement, it is a limited and constrained resource that is almost fully utilised globally. Around 90% of all iron ore slag is already being processed into GGBS each year. Therefore, any increase in the amount of Portland cement substituted with GGBS from existing stockpiles is unlikely to decrease global carbon emissions. While supplies of GGBS should continue to be fully utilised, the paper argues that unless overall supply expands, increasing the use of GGBS in one location is highly likely to result in a reduction in use elsewhere.
Timber
The benefits of using timber in construction have been considered at length. In fact, G&T produced an entire series about its use in the construction industry. When sourced sustainably and used in an appropriate and efficient way, timber is a versatile and renewable material[14] that could be used to replace carbon-intensive steel and concrete in construction.
An older technology that has seen renewed interest in academics and industry of late is transparent timber – a structural product with thermal insulation properties that can reduce the use of artificial lighting and lower energy costs.
Transparent Timber
Imagine buildings with the natural warmth and beauty of timber while enjoying the benefits of transparency. Transparent timber, developed by removing lignin (a light-absorbing component that makes up the cell walls) from treated and compressed timber strips and replacing it with a specific type of polymer, offers remarkable strength and transparency.
Transparent timber is emerging as a cutting-edge functional material with the potential to substitute traditional optical materials – such as glass and plastic – in various applications, including construction. Transparent timber retains the strength of normal timber but weighs less. Using load bearing, structural transparent timber panels affords architects more design freedom to let natural light into a building. It’s also possible to imbue the timber with certain desired properties.
One application being considered is embedding the timber in walls and ceilings with quantum dots (ie a collection of semiconductor atoms, a few nanometres wide, which fluoresce when exposed to UV light) to create light-emitting diodes (LEDs), providing indoor lighting. Equally, the timber could be painted with a thin layer of polymer, allowing the timber to act as an electrochromic window with light being blocked out when a current is run through the timber.
The use of transparent timber has several advantages for the environment. Timber is a renewable resource that can absorb and store CO2 from the air. It can also decompose naturally, unlike transparent plastics derived from fossil fuels such as polypropylene, PVC, acrylic, polyethylene etc. According to a life-cycle analysis study conducted by the Indian Institute of Technology, transparent timber reduced ecological impact to the order of 107 compared to polyethylene, paving the way for it to be commercially adapted to replace the petroleum-based material.[15]
Compared to glass – the current see-through material of choice – transparent timber has greater thermal efficiency[16], reducing energy costs. Glass production also comes with a heavy carbon footprint, producing 22 million tonnes of CO2 in Europe and 95 million tonnes worldwide each year[17]. The potential carbon savings of switching to transparent timber could therefore be significant. Further advantages of transparent timber over glass include:
- Its ability to withstand stronger impacts (ie it’s shatterproof)
- It’s far more durable than glass
- It’s lighter than glass
- It’s more biodegradable than glass[18]
Despite having some sticking points[19], the material promises energy efficiency by allowing natural light to penetrate deep into buildings while maintaining insulation properties. This innovation has the potential to redefine architectural design and reduce the need for artificial lighting. The case for transparent timber therefore couldn’t be…clearer.
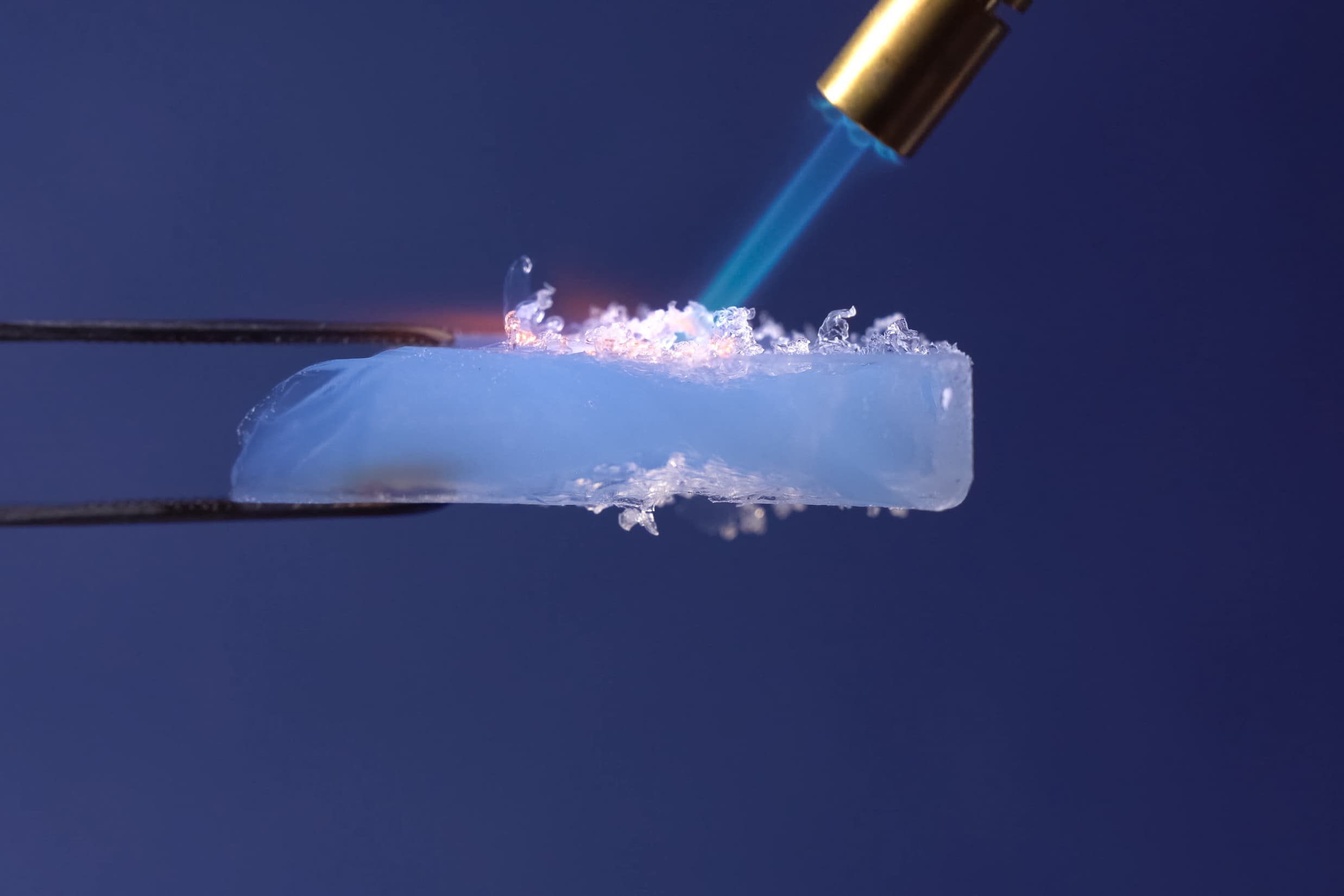
Aerogels
Sustainable, affordable Insulation with Aerogels
Another promising material for insulation applications is aerogels – a synthetic low-density, ultra-light material derived from a gel. The liquid component for the gel is replaced with a gas, bypassing the shrinkage and cracking experienced during ambient evaporation. This creates a solid three-dimensional nanoporous structure containing 80-99% air.[20]
Aerogels are essentially puffed-up sand, best described as being to sand as what a rice crispy is to rice! Often referred to as "frozen smoke" due to its translucent appearance, Aerogel insulation is incredibly efficient, providing superior thermal protection while being lightweight and eco-friendly.
Although aerogels were invented in the 1930s, the search for high-performance insulation in buildings has prompted growing numbers of manufacturers to turn to aerogel products. Aerogels offer several benefits, especially when space is at a premium.
Unmatched insulation
One of the most compelling features of aerogels is their unparalleled insulating capabilities. Despite their minimal weight, aerogels boast impressive thermal resistance. In fact, they are among the most effective insulators available and are used by NASA to insulate space shuttles and space suits. This property makes them ideal for maintaining comfortable indoor temperatures (ie by preventing thermal and cold bridging), reducing energy consumption and improving overall building efficiency.
Exceptional Strength and Durability
While aerogels may appear fragile due to their translucent and airy appearance, they are surprisingly strong and durable, capable of holding up to 2,000 times its weight in applied force[21]. Their nanoscale structure offers remarkable mechanical stability, enabling them to withstand significant pressure and stress. This strength makes aerogels suitable for various construction applications, from insulation in walls to load-bearing components.
Energy Efficiency and Sustainability
In a world increasingly focused on sustainability, aerogels align perfectly with the construction sector's eco-friendly goals. Their exceptional insulating properties reduce the need for energy-consuming heating and cooling systems, ultimately leading to reduced energy consumption and lower carbon emissions. Additionally, aerogels can be produced from a variety of materials, including silica and carbon, which are abundant and renewable, further enhancing their green credentials.
Versatile Applications
Aerogels' versatility extends to a wide range of construction applications, used in walls, roofs and windows in all sectors including residential and commercial buildings, refurbishments and energy efficient retrofits. As they can be made into an extremely thin film, they are a good insulation solution for small, hard to treat areas where space is at a premium and critical tolerances have to be achieved.[22]
Transparent versions can also be incorporated into windows (“aerogel windows”), enabling natural light to penetrate deep into buildings while providing excellent thermal insulation. Aerogels can even be incorporated into structural elements, enhancing their strength and reducing overall weight.
Challenges and Future Prospects
While aerogels hold immense promise, challenges such as cost, manufacturing scalability and moisture resistance must be addressed for widespread adoption in construction. Research and development efforts are ongoing to overcome these hurdles. In fact, recent developments have found more cost-effective ways to manufacture the material that could improve their uptake.
As the construction sector continues its journey towards sustainability and efficiency, aerogels emerge as a transformative material that aligns with these goals. With ongoing advancements and increasing awareness of their potential, aerogels are poised to redefine the way we build, ushering in an era of greener, more energy-efficient and resilient construction projects.
Smart Materials
Smart materials are perhaps best described as ones that can respond to various inputs, for example mechanical strain, changes in magnetic or electrical fields, temperatures, pH, light and moisture. These materials tend to be equipped with sensors and actuators that respond to changes in their environment.
Below, we outline just two examples of smart materials and how they are being used in construction, but many more show significant promise and could fundamentally change the way buildings are constructed in the future.
Shape-Memory Alloys (SMAs)
Shape-memory alloys (SMAs) can return to their original shape when subjected to specific stimuli (ie temperature change or mechanical stress), making them ideal for self-repairing structures.
SMAs have many potential use cases and can offer various benefits. One of these is seismic resilience, which means that buildings with SMAs in their structure can withstand earthquakes better. For example, reinforcing beam-column joint interfaces with pre-stressed SMA tendons or bars. The SMAs can absorb and dissipate the seismic energy, protecting the structure from damage. Another benefit is energy efficiency, which can be achieved by using SMAs in windows and façades. These SMAs can change their shape and openings to optimise natural light and ventilation, reducing the reliance on artificial heating and cooling.
Piezoelectric Materials
Piezoelectric materials are another class of smart materials that have gained prominence in construction. Piezoelectric materials can generate electricity in response to mechanical stress, and conversely, deform when subjected to an electrical field. This unique property opens up a range of applications in the construction industry, including energy harvesting, structural health monitoring and active vibration control.
For example, piezoelectric materials can be integrated into flooring systems to capture energy from footsteps and vibrations. This energy can then be converted into electricity and used to power sensors, lighting, or even feed back into the grid. This technology offers a sustainable way to harness energy in high-traffic areas.
Piezoelectric sensors can be embedded in building materials to monitor structural health continually. By detecting changes in strain, stress, or deformation, these sensors provide real-time data on a structure's condition, helping to identify potential issues before they become critical.
Piezoelectric materials can be used to mitigate vibrations in buildings caused by factors such as wind or machinery. By applying controlled electrical fields, these materials can counteract vibrations, enhancing occupant comfort and structural integrity.
Challenges and Future Prospects
While shape-memory alloys and piezoelectric materials offer promising benefits, there are still challenges to overcome, including their high cost, scalability and integration into existing construction practices. There are also concerns over their durability, reliability fatigue resistance, activation time and compatibility with other construction materials. Efforts are therefore ongoing to make these materials more accessible and practical for widespread use.
As smart materials like SMAs and piezoelectric materials continue to evolve, they are reshaping the construction industry. These innovative materials are not only enhancing structural integrity but also improving energy efficiency, sustainability, and overall building performance. As construction embraces the potential of smart materials, we can expect a future where our buildings are more resilient, efficient, and adaptable than ever before.
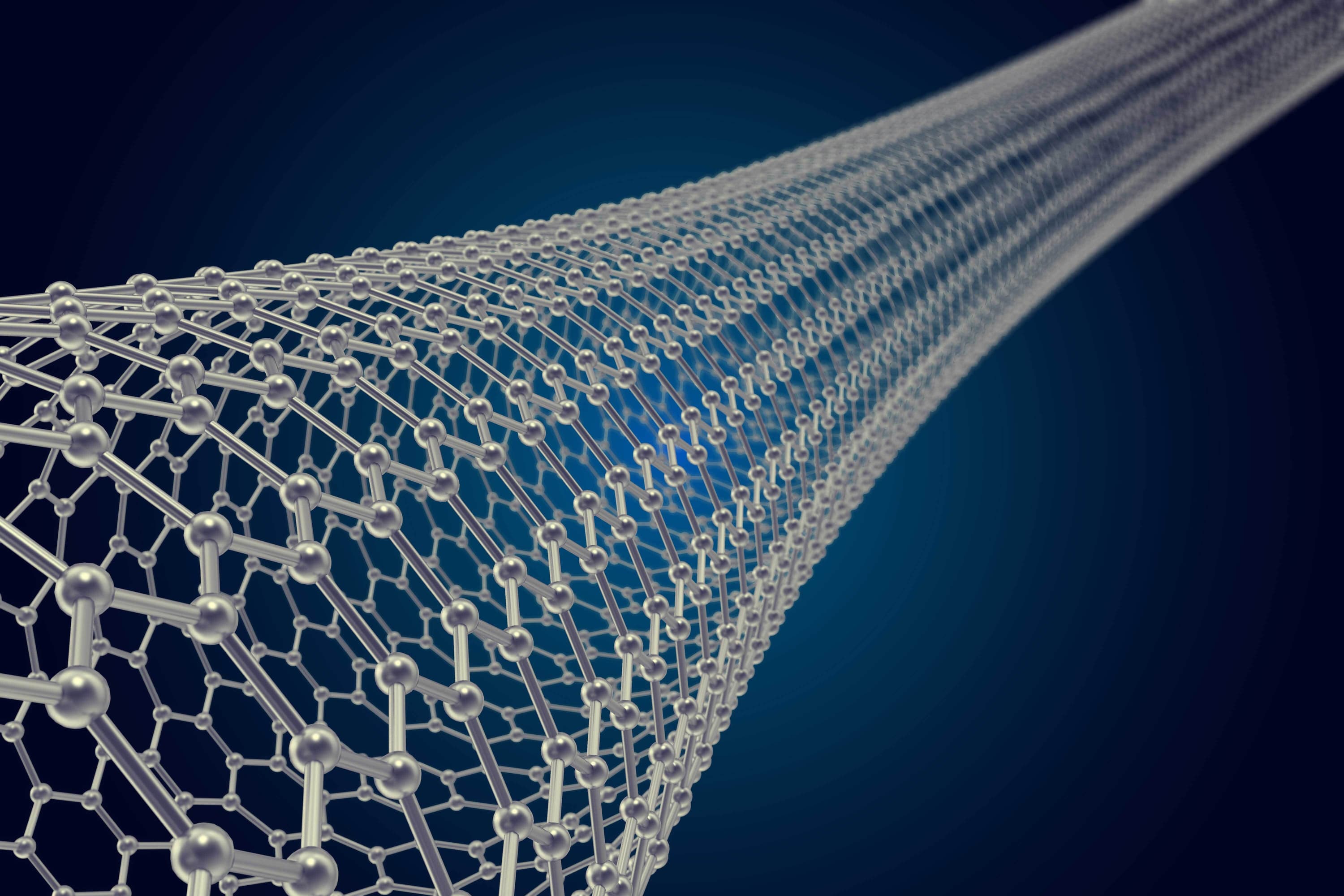
Nanomaterials
Nanotechnology, hailed for its transformative influence across various industries, is now making significant strides in the realm of construction materials. Despite being a relatively nascent field, it is increasingly recognised as one of the most promising technologies. The application of nanotechnology in construction materials is anticipated to yield positive impacts, presenting new avenues for innovation and enhancement in widely used building components.
Nano-engineered materials, such as carbon nanotubes and nanoparticles, can enhance the strength, durability and resilience of traditional construction materials such as concrete, steel, glass and timber. They can also be used to develop self-cleaning surfaces that repel dirt and pollutants, contributing to cleaner and more sustainable urban environments.
By manipulating traditional materials on a nanoscale, we can create fundamentally different properties and behaviours. Some of the major applications in key construction materials are summarised in the table, below.[23]
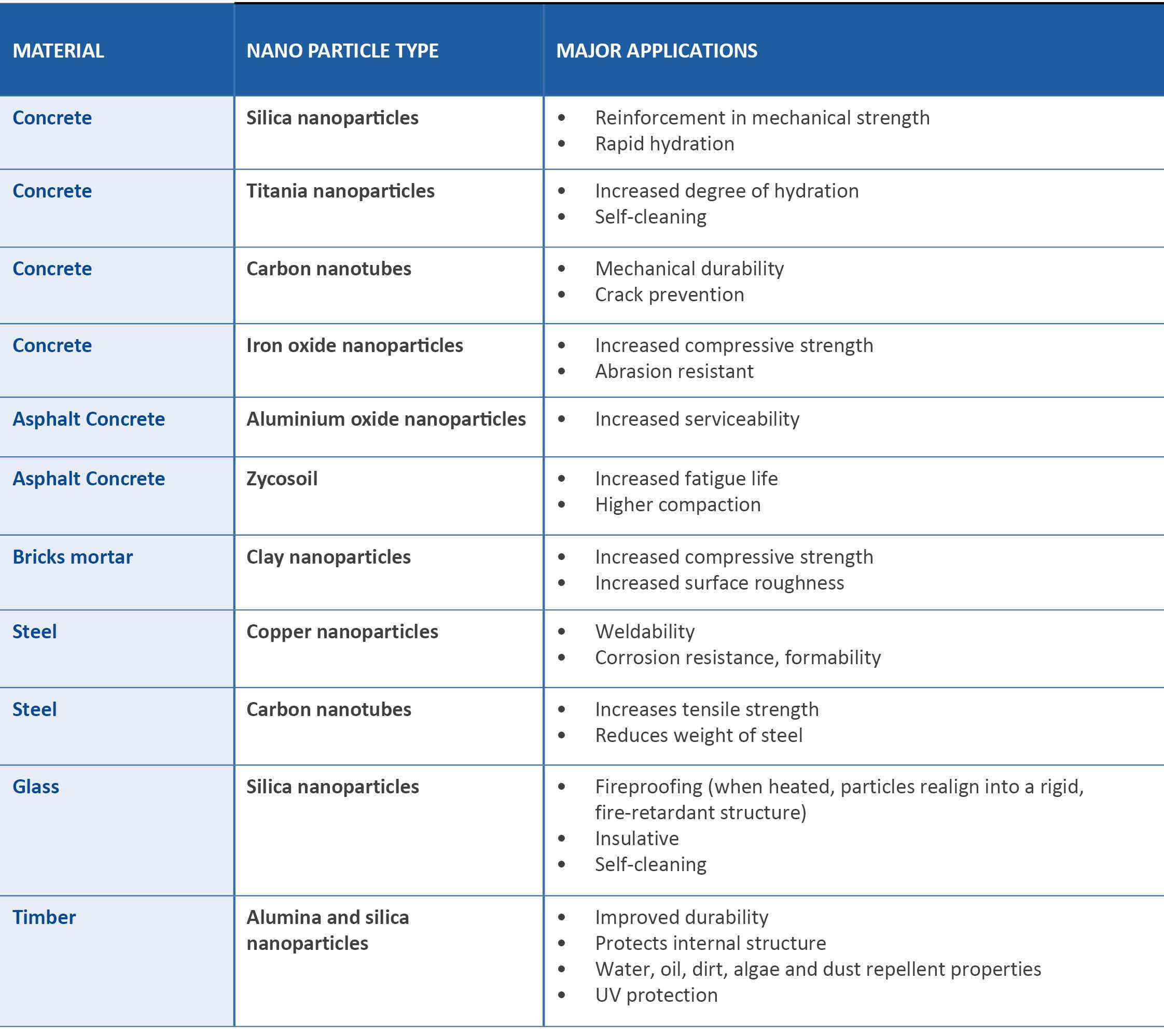
Mixing nanoparticles with these materials produces an array of benefits. From making concrete and glass that's fire-protective, to giving strength to timber and steel at much lower densities, and even making our glass and cement self-cleaning, nanotechnology is helping us build a safer, cleaner and more efficient world.
The sustainability aspect of nano materials also shouldn’t be understated. Raw material consumption is one of the biggest problems from a sustainability perspective, but nanotechnology can help decrease consumption by increasing the durability and life span of the materials used in construction. Carbon emissions can also be reduced by the addition of nanoparticles during material production as well as by improving the energy conservation properties of the materials and the buildings in which they are used.
Despite the promising potential of nanomaterials in construction, their use has been hindered by certain headwinds. Although the production of nanoparticles has caught up with supply in recent years, regulation is still lagging. Health, safety and environmental considerations of production, product application and end of life disposal have struggled to stay astride of the industry. The potential long-term effects and toxicity of nanoparticles used in various industries underscore the need for careful consideration, oversight and regulation to address their altered interactions with biological systems.
Conclusion
Most of our built environment has been constructed from a relatively narrow selection of tried and tested materials. Historically, there has been a strong sense of entrenched conservatism with regards to incorporating new materials and material technologies, but there are valid reasons for this. There are often issues with updating design codes, product testing, as well as insurance barriers. But in a world that is consuming resources at an increasingly unsustainable rate, a wider array of novel and re-engineered materials solutions is needed.
Many of the materials technologies explored in this article are still in their infancy, with relatively few proven use cases demonstrating their effectiveness and viability in the construction industry. Others simply take familiar materials and combine them in new ways. However, the commitment to decarbonise society has spurred interest in exploring new (and in some cases, not-so-new) materials that are potentially smarter, more efficient, and more sustainable.
The construction industry has become more willing to adopt cutting-edge materials technologies, as long as there is evidence to support their claimed benefits. However, whether the benefits are financial, performance-related, or environmental, they need to be significant to drive adoption. As the construction sector continues to evolve, we can expect to see more groundbreaking developments that will shape the way we build our cities and homes in the future.
References:
[1] https://www.bath.ac.uk/case-studies/using-bacteria-to-create-spontaneous-self-healing-concrete/
[2] https://sdgs.un.org/partnerships/self-healing-enzymatic-bio-concrete-fight-climate-change#:~:text=Our%20company%2C%20Enzymatic%20Inc.%20has,(CA)%20in%20construction%20material
[3] https://www.checkatrade.com/blog/trade/self-healing-concrete/#:~:text=Cost%20of%20self%2Dhealing%20concrete,-One%20of%20the&text='%20And%20although%20the%20longevity%20and,upfront%20costs%20are%20still%20higher.
[4] Adding bacteria and water-absorbent polymers drive up the cost.
[5] https://www.ribaj.com/intelligence/decarbonising-concrete-global-emissions-climate-change#:~:text=Research%20by%20think%20tank%20Chatham,%2C%20which%20generates%20about%202.5%25.
[6] https://www.converge.io/blog/how-to-reduce-embodied-carbon-in-concrete#:~:text=Most%20of%20concrete's%20embodied%20carbon,to%20approximately%201450%C2%B0C.
[7] Conventional mixes using 100% OPC cement will account for an even higher proportion of embodied carbon.
[8] https://www.seratechcement.com/our-technology
[9] https://www.akt-uk.com/latest/crinkle-crankle-concrete-story-within/
[10] Both of which are industrial by-products with a much lower carbon footprint than Portland cement.
[12] The long-term research programme was co-funded by Laing O’Rourke and Innovate UK and was in collaboration with the University of Cambridge and Sheffield University’s Advanced Manufacturing Research Centre (AMRC). The programme proved that a range of low carbon concrete options can be successfully deployed on projects as a like-for-like substitute for traditional concrete.
[13] https://www.istructe.org/resources/guidance/efficient-use-of-ggbs-in-reducing-global-emissions/
[14] Timber is technically renewable; trees that have been cut down can be replaced with new trees. However, to be truly renewable, a resource must be replaced within the same timescale it is being used up – otherwise its reserves will be reduced. That’s why timber isn’t renewable unless it is sourced from sustainable, responsibly managed forests.
[15] https://interestingengineering.com/science/transparent-wood-the-alternate-to-plastics
[16] In a study published in the journal Science of The Total Environment, producing transparent timber is approximately five times more thermally efficient than glass.
[17] https://cinea.ec.europa.eu/news-events/news/how-life-reducing-emissions-glass-production-2022-03-16_en#:~:text=However%2C%20glass%20is%20made%20in,are%20required%20to%20make%20glass.
[18] https://interestingengineering.com/science/transparent-wood-the-alternate-to-plastics
[19] Making transparent timber uses lots of energy and some environmentally harmful chemicals. Also, the liquid waste made during this process proved difficult to recycle.
[20] https://www.aerogel.org/?p=1058
[21] https://www.thermablok.co.uk/
[22] https://www.designingbuildings.co.uk/wiki/Aerogel_insulation_for_buildings#:~:text=Aerogels%20are%20often%20cited%20as,Cavity%20insulation.