Construction
- RIBA’s Future Trends Survey shows that prior to the Ukraine crisis, architects were positive about workload growth over the next three months. All sectors, practice sizes and regions demonstrated a positive outlook, with 32% of practices overall expecting workloads to increase. Just 10% of practices said they expected workloads to decrease, while 58% expect them to stay the same. Although the overall workload index grew five points to +23 in February, the data was collected prior to Russia’s invasion of Ukraine so does not give insight into any secondary, economic effects the profession may feel.
Source: RIBA
According to Adrian Malleson, RIBA’s head of economic research and analysis, the picture of economic stability might be short-lived. Malleson said the conflict would compound existing supply and inflation issues, adding that rapidly increasing energy prices demonstrated the need for the UK to implement a “well-funded and designer-led retrofit programme”.
- UK construction output rose by 1.4% in January month-on-month, reaching its highest level since September 2019. While the Ukraine crisis may slow growth, the latest figures were a sign that supply chain difficulties were easing. Output is now 1.4% above February 2020 pre-pandemic levels, but the recovery has been mixed. Output in the private commercial sector, for example, was nearly 28% lower in January 2022 than it was before the pandemic while output in the infrastructure sector has grown by nearly 40% since February 2020. On a month-on-month basis, repair and maintenance work drove output growth (rising by 4.6%). However, new work output contracted by 0.8%, with new infrastructure output values dropping 4.7% and public non-housing work by 9.1% month-on-month.
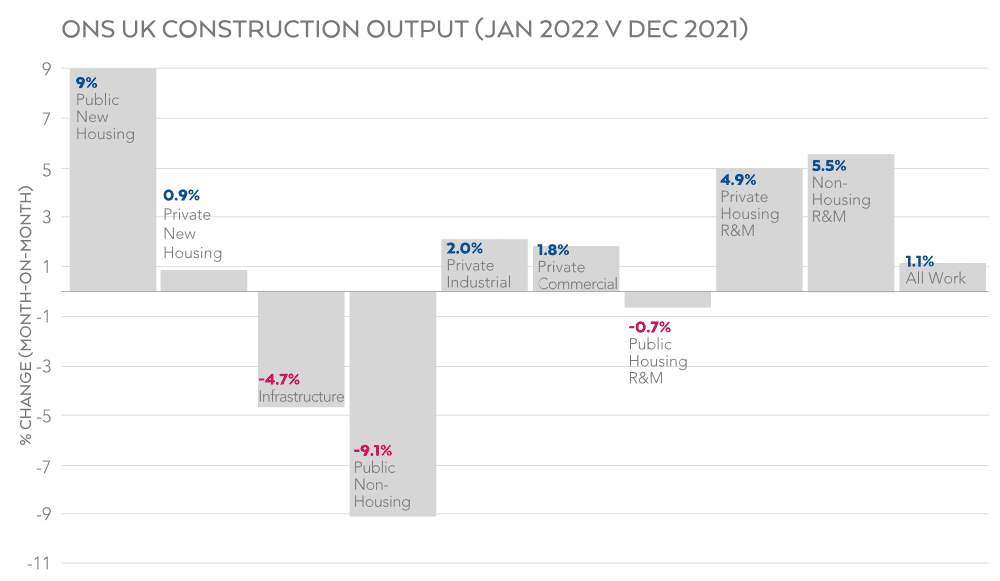
Source: ONS
- Russia’s invasion of Ukraine has replaced COVID-19 as the top risk to global supply. G&T has recently published analysis of the potential impact of the Russia-Ukraine conflict on supply, demand and tender pricing. Key points include:
- The greatest impact to UK construction from the conflict is expected to be spiking oil and gas prices
- This will have a knock-on effect for most construction materials, increasing input costs and tender prices, as well on shipping and logistics costs
- Although the UK does not rely heavily on Russian commodities, global inflationary pressures will impact UK inflation
- Sanctions imposed on Russia are likely to be long-term, creating further supply chain disruption and compounding any lingering pandemic-driven supply issues
- Materials with energy-intensive production processes (eg concrete/cement, steel and aluminium) will experience the greatest inflationary pressures
- The level of tender price inflation will depend on how sustained disruption to global energy supplies is, the severity of sanctions/restrictions imposed on Russian exports and how quickly supply chains can adapt and diversify sources of supply
- The IHS Markit/CIPS UK Construction PMI registered 59.1 in February, up from 56.3 in January to signal the strongest rise in output since mid-2021. The headline index has now posted above the neutral 50.0 threshold in each of the last 13 months. Building companies commented on the strongest rise in output amid stronger client confidence and work on new projects commencing. Construction companies continued to report widespread supply constraints and rapidly increasing input costs, though the rate of inflation in the latter was the least severe for 11 months. While companies remained highly upbeat about their growth prospects for the next 12 months, ongoing disruption dampened the year-ahead outlook for activity, causing the Future Activity Index to hit its lowest level since January 2021. The Russia-Ukraine conflict could further diminish client confidence in March’s survey.
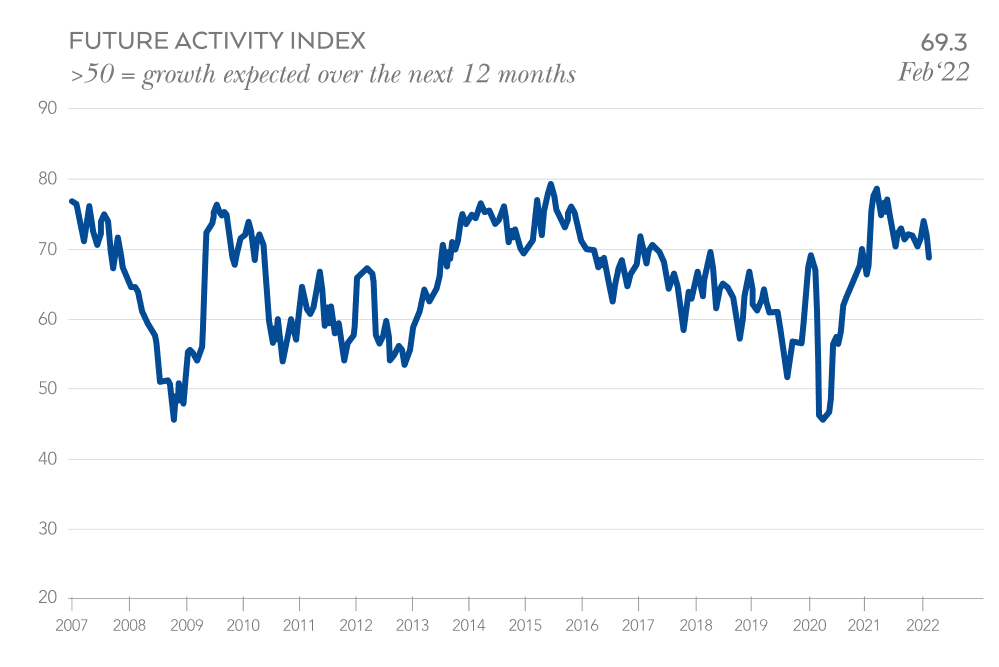
Source: IHS Markit
- In the National Infrastructure Commission’s recently published Infrastructure Progress Review 2022, the NIC suggests that the Government is not on track to deliver infrastructure changes to hit net zero by 2050, to level up the UK or improve climate resilience. The report assesses the current state of infrastructure policy and delivery in pursuit of stated Government aims. It states that while gigabit broadband coverage and renewable electricity capacity have continued to increase, and the UK Infrastructure Bank has been set up as promised, local transport improvements and the housing retrofit drive to improve the energy efficiency of buildings have not materialised. The 2022 Progress Review sets out 10 priorities for the year ahead, including the need to accelerate the roll out of EV charging points to ensure the 2030 date for the end of the sale of new petrol and diesel cars remains viable.
Client & Contractor News
- Balfour Beatty plans to continue with its UK building business despite it being in the red for the second year running. The business accounts for around £800m of Balfour Beatty’s turnover, but snags at several residential schemes in the capital have resulted in losses. Chief executive Leo Quinn said a number of fixed-price schemes have been plagued by rising material and labour costs, helping send the UK construction division to a £2m loss (down from a £26m loss the previous year). With regard to Balfour’s core capability and competency – very large infrastructure projects – it noted that, “There is a decade of infrastructure growth coming up and we are superbly positioned for the 2030s.” Commenting on the impact of the Ukraine crisis, Quinn added:
“Anything oil-based will go up. Inflation is one of the big worries at the moment. It is moving so rapidly. There are not too many people in the industry who remember the inflation of the 70s but we have to take a responsible approach to hyperinflation. Companies can absorb 1 or 2% but when it’s 10, 20, 30% that is beyond reasonable.”
- According to Kier’s latest set of results, revenue at the firm’s biggest division (its construction arm) has been hit by the impact of rising costs. Rising costs have meant delays to project starts and Kier noted that clients are taking longer to sign off on jobs, which has blunted turnover. Revenue from its construction business fell by a quarter in the six months to December 2021 as some clients took a second look at jobs. The slump in revenue meant operating profit at construction fell from £30.7m to £12.8m.
“Headwinds are causing reappraisals of business cases which is causing some delays on getting our jobs going, particularly in our construction business…Clients need to go back and get approvals in the wake of increased costs.”
- Skanska has signed a £235m contract to redevelop the old House of Fraser department store on London’s Victoria Street. The building will be demolished and replaced as part of a wider £750m development by Canadian-owned property investor BentallGreenOak (BGO), but Skanska has signed a £235m contract with Welput, the specialist central London office fund managed by BGO, to deliver a mixed-use commercial development at 105 Victoria Street. No fossil fuels will be used during construction or operation of the new 470,000 sq ft, all-electric building. Skanska will deploy innovations in ultra-low carbon construction to ensure the carbon emitted through the construction cycle will be offset within six years of the new building’s operation in comparison to the retention of the existing building.
- Some contractors have warned clients that they will be unable to fix prices on projects for the next few months. Material price inflation is set to rise in light of the war in Ukraine. Putting further pressure on contractors that were struggling to keep costs within agreed budgets. Across the board material price rises, combined with some wage inflation, have left firms such as Osbourne to stop looking at taking fixed price jobs. Another major Tier 1 firm said that clients are also reluctant to fix prices - but for different reasons to contractors:
“Clients are worried because they don’t want to fix at too high a price, only for things to calm down and they’re locked into a contract where they’re effectively overpaying. I think we’ll see a lot of fluctuating contracts, where prices are struck according to industry-recognised measurements.”
- Research conducted by Lloyds Bank Commercial Banking found that the pandemic exacerbated late payments in construction. More than two-thirds of the 173 surveyed construction firms that said they had seen a change in customer behaviour since the beginning of the pandemic, experienced slower payments. Just over a quarter of surveyed businesses said it now takes customers more than 30 days to settle invoices, with 33% of debtors citing cashflow pressures and 28% citing late payments from their own customers as their reasons for paying late.
Materials & Commodities
- Brick manufacturer Forterra has announced double digit price increases from the beginning of April. This follows a 16.5% hike at the end of 2021. Forterra said that with most raw materials being sourced internally, its brick business was insulated to a degree from the worst inflationary pressures until energy prices increased suddenly in the Autumn. The conflict in Ukraine has added further uncertainty to energy prices while security of energy supply has become an increasing concern. In its annual results, Forterra’s revenue was up to £370.4m in the 12 months to 31st December 2021, from £291.9m the prior year. Forterra made a pre-tax profit of £56.8m after a loss of £5.4m in 2020. The firm said the new build and repair and maintenance markets have helped drive the recovery from the pandemic.
- According to the CLC’s latest Product Availability Statement, further price rises are on the horizon following Russia’s invasion of Ukraine. Manufacturers have increased prices by 5-10% on average so far this year, whilst more energy-intensive products have risen by as much as 20%. Raw materials shortages, along with rising energy, freight and labour costs, were identified as the root cause of higher prices. Global trade will be significantly affected but it is unclear how this will affect materials supply in the UK. While Russia, Ukraine and Belarus accounted for just 1.25% of building products imported into the UK last year, some product components could be exposed to inflation through raw material price increases. These materials include aluminium, copper, bitumen, pig-iron and iron ore used in the manufacture of steel.
- British Steel has blamed rising electricity costs on its recent £250/tonne hike on all new orders of structural steel sections. Commodity and energy price volatility has significantly increased the key input costs in the steel manufacturing process. This, combined with significant disruption to international trade flows, were cited as the key reasons for the c.25% jump. British Steel’s highest one-off increase has resulted in steel section prices of more than £1,000/tonne. The recent hike follows a 51% increase in fabricated steel prices in the year to January 2022, according to BEIS data. This will push up costs on many UK construction projects, including the UK’s largest infrastructure project – HS2. British Steel also added that it could not provide price guarantees for production beyond the middle of April because of the rising costs, highlighting just how uncertain and unstable the situation is.
UK Economy
- According to IHS Makit’s UK Business Outlook Report for March 2022, nearly two-thirds of UK manufacturers and service providers expect output to increase over the next 12 months, but many anticipate record increases in costs and selling prices over this period. Company profits are likely to be squeezed as the cost-of-living crisis intensifies. Strong employment growth forecasts amid labour shortages and problems retaining staff will also put a strain on profits. The latest Business Outlook survey was largely conducted prior to the invasion of Ukraine, but even so nearly 65% of firms reported plans to increase their charges in 2022. The surge in energy prices and additional inflationary implications of the conflict will only add to output price expectations.
- The chancellor Rishi Sunak has said that, if imposed, an EU-wide embargo on Russian oil and gas would cause at least £70bn of damage to the UK economy – the equivalent of 3% of UK GDP. Due to its dependence on Russian hydrocarbons, the EU has said that it will not follow the UK and US in banning imports. Instead, the EU will cut imports over a period of time. Despite the UK importing relatively little Russian oil and gas, an immediate EU ban would likely tip economies across Europe into recession, including the UK. The resulting global supply shock of an EU ban would likely lead to a “deeper near-term hit [to output] followed by a much slower recovery thereafter” for the UK, according to Sunak.