Stora Enso, a global manufacturer of renewable packaging, biomaterials, paper and wooden constructions, has developed a new flexible, modular wooden office concept.
Developed in partnership with G&T, Ramboll, Scott Brownrigg and JLL, the concept provides guidance and support to architects, engineers and developers looking to design flexible, cost-effective modular office buildings using pre-fabricated wooden building components.
A major challenge facing UK construction is balancing growth with sustainability. On the one hand greater volumes of housing and major improvements to infrastructure are required, but on the other the Government has set an ambitious target to reduce emissions by 50% in the built environment by 2025 as part of its Construction 2025 industrial strategy.
Meeting this challenge will require a substantial and rapid decrease in carbon-intensive construction materials whilst increasing low-carbon alternatives. Stora Enso believes that one way of moving towards carbon neutrality and achieve compliance with these sustainability ambitions lies in building with low-carbon, renewable and recyclable materials such as wood.
Stora Enso’s core belief is that everything that is made from fossil-based materials today can be made from a tree tomorrow. Whilst their wood product range covers all areas of construction, their latest concept focuses on office buildings.
WHY WOOD?
In a word, ‘sustainability’. Stora Enso’s main raw material is renewable wood from sustainably-managed forests, and they work to ensure that more trees are planted than harvested.
Stora Enso says that construction materials account for 40% of all materials used in the world today.
Together, building and construction are responsible for 39% of all carbon emissions globally, with operational emissions (from energy used to heat, cool and light buildings) accounting for 28%. However, the remaining 11% comes from embodied carbon emissions or ‘upfront’ carbon that is associated with materials and construction processes throughout the whole building lifecycle [1]. In the UK this figure is even higher, with construction embodied carbon accounting for roughly 19% of our total greenhouse gas emissions [2].
According to Sebastián Hernández, R&D Manager for Building Concepts at Stora Enso, using responsibly and sustainably sourced massive wood products such as Cross Laminated Timber (CLT) and Laminated Veneer Lumber (LVL) instead of steel and concrete can reduce CO2 emissions by up to 75%.[3]
The thermal mass provided by Stora Enso’s wood products help reduce temperature peaks and improve the energy performance of the building. Not only does wood improve a building’s energy efficiency and reduce operational carbon emissions, it also absorbs and stores carbon from the atmosphere over its lifecycle. At the end of its lifecycle the products can be reused, recycled or used for energy production.
Wooden workspaces also provide health and wellbeing benefits. Stora Enso refer to a study[4] which found that natural design in the workplace can increase the health and wellbeing of employees by 13% and their productivity by 8%. Offices constructed from wood can help employees feel more connected to nature and forge positive associations with their workplace. The end result is improvements in employee retention and higher levels of concentration, wellbeing, happiness and productivity in the workplace.
Furthermore, building envelopes based on massive wood products can improve indoor climate and improve air quality. By absorbing and releasing moisture from the air, wood has a buffering capacity that can stabilise moisture levels and reduce uncomfortable highs or lows in humidity. It is also an effective way to avoid moisture-related problems that can lead to poor indoor air quality.
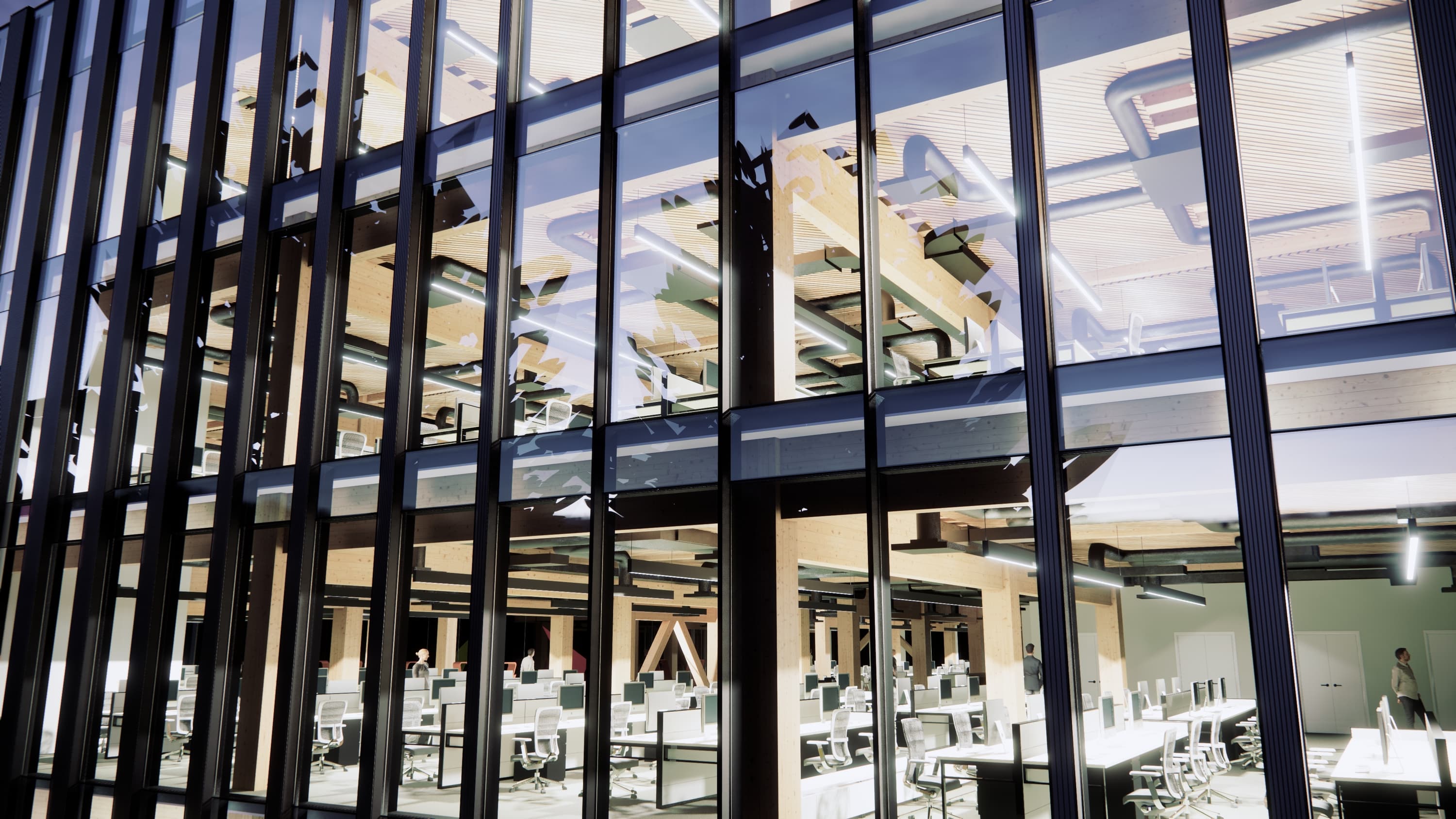
WHAT ELSE DOES WOOD BRING TO THE TABLE?
Wood, being five times lighter than concrete, lowers transportation costs and associated emissions. In fact Stora Enso measured that a building made from massive wood requires, on average, just 15% of the transport cost compared to a standard concrete building.
Using wood can also reduce the weight of a building, resulting in reduced sub-structure and foundation requirements. Some of the lighter massive wood products can be installed with mobile rather than heavier and more expensive tower cranes. Also from a cost perspective, projects can benefit from a faster erection time, a more reliable programme and more efficient logistics.
Furthermore, Stora Enso suggest that a longer service life can be achieved with wood, noting that wooden buildings are easier to change and adapt to future requirements and different uses which can increase the service life. They argue that because the products are prefabricated in controlled factory conditions the quality of construction can be very high, resulting in a reduced demand for renovation and refurbishment over the building’s life cycle.
THE CONCEPT
Stora Enso’s concept outlines some of the possibilities when it comes to constructing efficient office buildings from wood. The guide focuses on how to use massive wood products such as CLT and LVL in a cost-effective way and how the concept can be adjusted to meet specific project or market needs.
Their concept stems from a collection of over 5,000 calculations that Stora Enso has done over the past year, culminating in the publication of the guide. The high-level guide is intended to inspire stakeholders to use wood in future projects and acts as a good starting point that can be subsequently developed.
All components can be designed for fire, acoustics and thermal and can be machined to various dimensions, making it very flexible for designers. Its flexibility allows you to build almost any type of building and the clip-together system means there is less bespoke work to do on site. Glued in factory conditions the wood components provide high load-bearing capacity outperforming the strength-to-weight ratio of both steel and concrete.
The publication provides guidelines and basic principles to architects to help them apply the building concept to various types of office buildings. It also includes information on building structure (eg grid planning, structural framing, number and size of columns required and connection philosophy), acoustics and sound insulation, fire safety, heating ventilation and cooling strategy and finally economics.
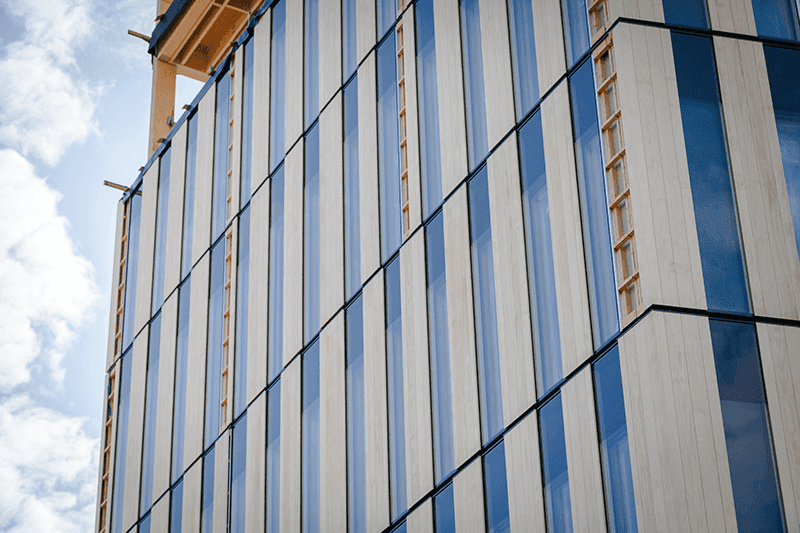
COST SAVINGS
Cost is always a fundamental consideration when deciding on structural frame material and core. The manual provides case studies showing examples of wooden office buildings that can enable reduced construction programmes, site overheads (preliminaries) and financial holding costs (ie costs relating to a portion of time when a project is held up) when compared to conventional construction methods.
Using timber can reduce construction times in the production phase by as much as 20-30% due to a better “follow-on” process. As touched on earlier, it can also reduce the weight of the whole building so that foundation requirements and therefore sub-structure costs are lower.
But all of this does not necessarily make timber a low-cost alternative. The concept compares the cost of CLT, LVL concrete and steel constructions across three different office building types in London. Whilst foundation and CAT A fit-out costs are generally lower for CLT and LVL constructions than they are for concrete and steel, the build cost for other aspects of the building, such as the structural panels on the main frame beams in the upper floors, can be higher.
It is important to weigh any cost premium against the benefits gained from a reduced construction programme, lower site overheads (preliminaries) and financial holding costs compared with conventional construction techniques. The publication suggests that using wood can reduce on-site assembly time by up to 70% and this can bring substantial cost-savings to an investor or developer. It also means a quicker return on investment can be achieved.
The faster construction time comes from pre-fabrication and whilst steel and concrete can be pre-fabricated, wood is lighter and therefore easier to lift and move on site.
Having seen the potential benefits of this sustainable technology G&T has been costing and delivering mass timber buildings for many years. When Stora Enso approached us with the opportunity to be a part of this informative concept manual by assisting them on construction costs, we were eager to work with their experienced design team once again by adding our expertise on the subject.
OTHER ADVANTAGES
In the launch webcast Stora Enso noted that because they use the latest in BIM and manufacturing technology, the build process can be more accurate and the build programme more predictable.
Wooden office buildings are also a differentiator, the renewable nature of the materials used in their construction can appeal to investors and occupiers that have ecological values and a carbon-neutral sustainability agenda.
On site using prefabricated wood materials can reduce time, space and noise disturbance. Massive wood buildings are one of the cleanest and quietest forms of construction as they remove the need for most wet trades and produce nearly zero-waste on site.
Due to the lighter weight of wood compared to other construction materials developers can build on softer ground which could open up more potential sites for development.
TAKE-UP
Low carbon alternatives such as wood have, thus far, not been used in the construction of office buildings at scale. Reasons for this generally revolve around risk. Stakeholders are cautious about using novel materials or concepts, believing them to be too risky, but also because they can be more costly and difficult to use. They can also be subject to insurance and legal constraints that can act as a barrier to widespread adoption.
Historically, steel and concrete have been the default structural frame material for tall office buildings. The combustible nature of wood, along with its tendency to bend, warp and soften, have in the past steered developers away from its use in office buildings. Now, with the advance of engineered timber solutions, many of these concerns have been addressed.
In their concept, Stora Enso indicate that fire safety in buildings relies strongly on the design and engineering, and less on the properties of the structural material used. Timber-based components can be designed to meet resistance standards set by most building regulations across Europe by, for example, using lining boards and fire-separating structures such as encasing and shaft penetration sealing. Sprinklers are also likely to be used for any mid-high rise office buildings, ensuring that the two-hour fire resistance period can be met.
Height has also been a challenge, but Stora Enso suggests that for taller buildings (9+ storeys) that are typically beyond the capabilities of CLT walls and braced timber bays, concrete cores can be used as a secondary structure to achieve stability. Stora Enso say that using this hybrid system means that it would be feasible to build to 80 storeys.
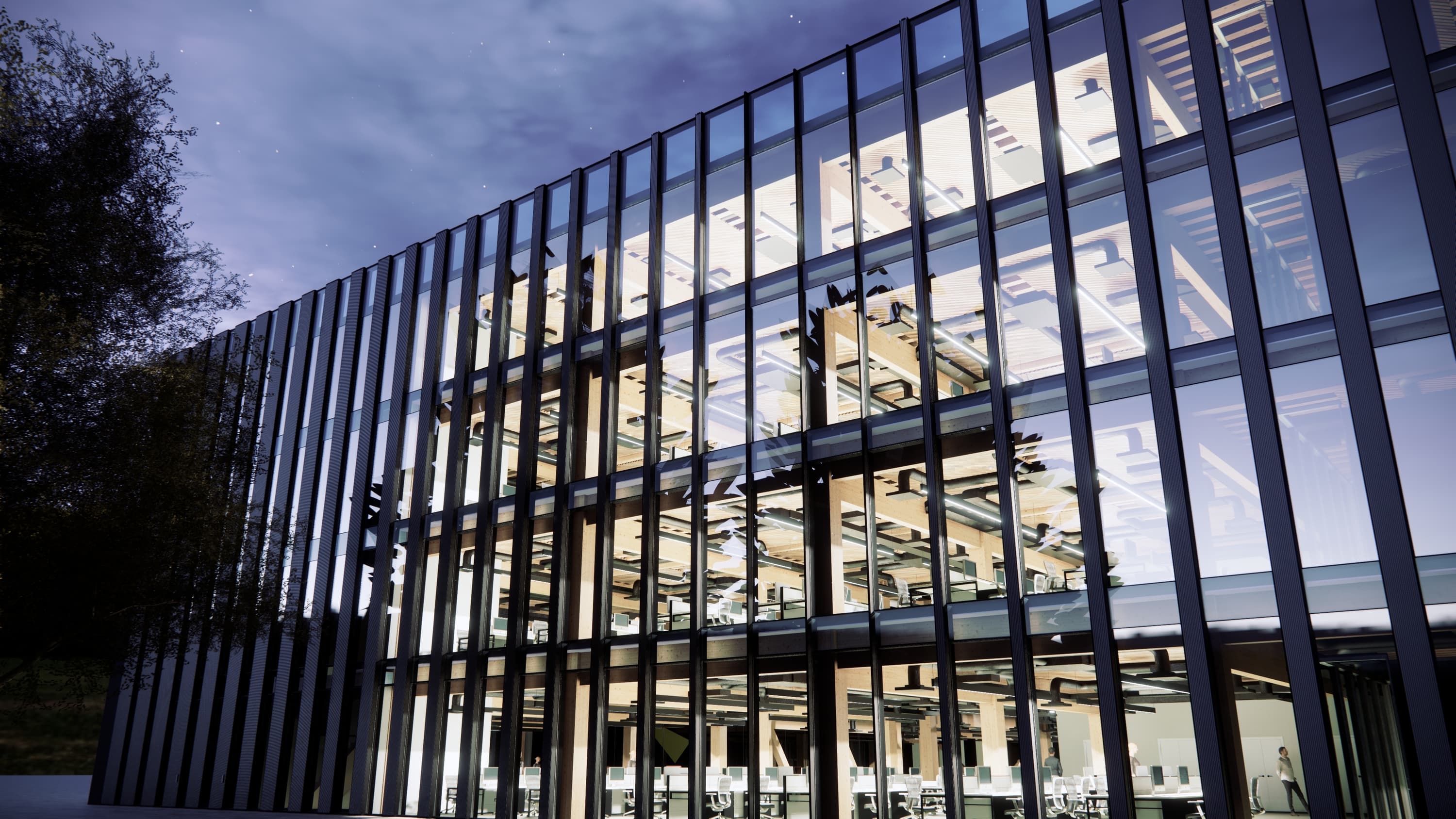
To read more about the concept and download the design manual visit the website.
Further information
Alongside the manual Stora Enso has launched a ‘concept hub’, allowing stakeholders to explore the various parts of the building in more detail. They also have an online design tool to help users understand where each element is supposed to go on site and are currently piloting an acoustics tool which allows stakeholders to test sound insulation between different constructions.
See these elements in action and visit the ‘concept hub’.
[3] Sebastián Hernández, R&D Manager for Building Concepts at Stora Enso
[4] KNOW Andrew, PARRY-HUSBANDS Howard, Workplaces: Wellness + Wood = Productivity, Pollinate, Forests and Wood Products Australia, February 2018