The Government’s bold new life sciences vision, as set out in its recently published 10-year strategy[1], will forge a path to build on its pandemic response and solve some of the biggest and most pressing healthcare challenges facing our generation.
The launch of the Life Sciences Investment Programme will bring an additional £1bn of funding to the sector and will help address seven critical healthcare missions that focus on preventing, diagnosing, monitoring and treating disease early, using innovative clinical trials to develop breakthrough products and treatments quickly to help save lives, and accelerating the development and adoption of new drugs, diagnostics, medical technology and digital tools. But with a current shortfall of R&D space in the UK, commercial developers and public sector bodies may have to re-evaluate their existing assets to meet that demand.
Introduction
The purpose of this article is to provide an overview of the UK Life Sciences sector, introducing what this means and providing a high level summary of the types of research labs that are found within a life science building.
The article provides an explanation of the different categories of labs, what types of space are usually found in a life sciences building and what special characteristics a building housing the life science facilities must have.
We consider whether it’s possible to convert existing buildings into life science developments or whether new build developments are preferable. We also suggest some ways to future-proof new commercial office developments to allow for future flexibility in adapting or fitting them out as life science buildings.
What are Life Sciences?
The life sciences industry represents one of the dominant economic sectors in the UK. ‘Health life sciences’ refers to the application of biology and technology to health improvement, including biopharmaceuticals, medical technology, genomics, diagnostics and digital health. It has the advantage of very high productivity compared to other sectors and generates a wide range of products including drugs, medical technology, diagnostics and digital tools as well as products for consumer health.[2]
The research and development to support the product development takes place in buildings which have a combination of traditional office environments, collaboration spaces, scientific laboratories and more. This is “life sciences”.
The UK life sciences sector has proven itself to be a crucial pillar of the UK economy - the sector generated almost £81bn in annual turnover and employed over a quarter of a million people across the country in 2019.[3]
The global COVID-19 pandemic has had a profound impact on the already flourishing industry, with growth in this sector accelerating. The pandemic has required a global effort to research and develop vaccines in life sciences labs. These same labs have also had to develop testing kits, producing Polymerase Chain Reaction (PCR) and Lateral Flow test kits which needed to be rolled out at scale. Both the vaccines and testing kits were delivered in record breaking time due to the combined efforts of the life science sector and the dedicated teams around the world. In fact, the COVID-19 vaccine was the fastest developed vaccine in history.
To emulate the success of the UK Vaccines Taskforce in developing and rolling out the Oxford-AstraZeneca vaccine, a co-developed roadmap has been provided in the form of the UK’s ‘Life Sciences Vision’. Hoping to solve a number of major health challenges ranging from dementia and cancer treatment, the Vision set out provides a new blueprint for how government, the NHS and industry can work together to deliver the next generation of therapies, diagnostics and insights to improve patient health. However, in order to deliver the Vision and cultivate growth in the sector, the UK needs to onshore the manufacture and commercialisation of breakthrough products. This will require the delivery of more commercial labs and R&D-related workspace but with analysis from Savills[4] showing a dearth of new lab space coming through in the short-term pipeline, other commercial buildings may have to be adapted to provide the much-needed life sciences space. Building new research and lab facilities can be a slow and carbon-intensive process. As we explore below, refurbishing existing office space can potentially offer a faster and more efficient solution.
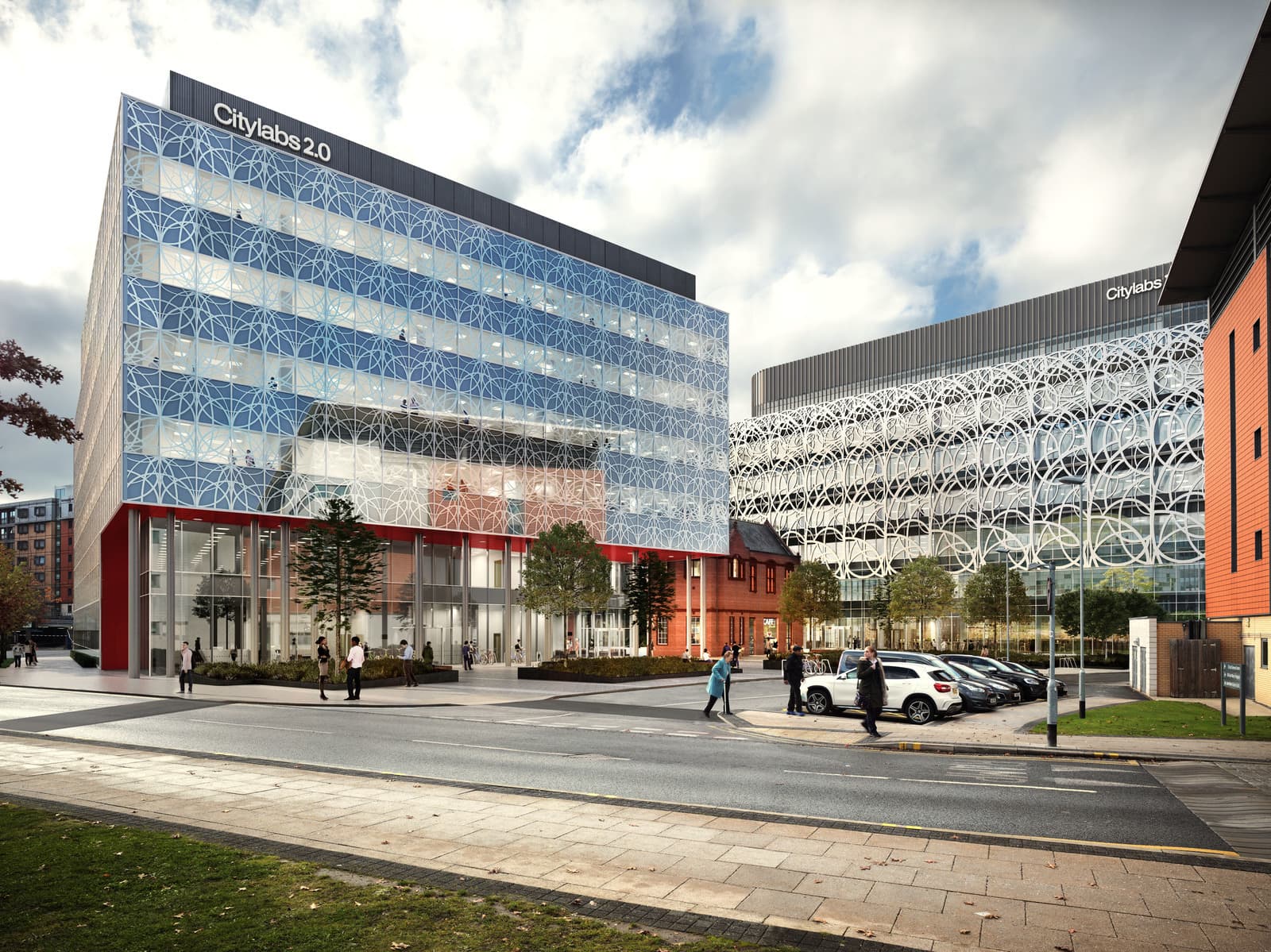
Citylabs 2.0 - G&T provided Cost Management and Construction & Property Tax Advice
Types of lab
There are two basic types of labs that sit within a life sciences building and both are required to undertake and document the research and development of medicines, vaccines and the like.
Wet Labs
Wet labs are for manipulating liquids, biological matter and chemicals. The function, use and equipment in the space is specific to the research and the biosafety levels required. Think of a room full of beakers, chemical concoctions and researchers wearing PPE[5] .
Dry Labs
Dry labs are focused on computation, physics and engineering. Think of a room full of computers, whiteboards and researchers wearing normal clothes and no PPE[6]. These spaces are more traditional and are akin to collaboration spaces used for research and development.
The science that begins in the dry lab is often confirmed in a wet lab. However, sometimes the results achieved in a wet lab can contribute to continued research and development in a dry lab. Both types of labs play an important role in the advancement of the science, but each takes a different approach to research.
What type of space does a life science building need?
Like any other building, a life science building contains spaces dedicated to the activities of the user groups that the building is designed to accommodate. They are no different from a standard commercial office building at its most basic level, but with specific spaces designed to house more specialist tasks, equipment and labs within. The layouts need to give consideration towards the adjacencies of supporting spaces, along with how these are stacked at different levels. Below is a list, separated into two parts, outlining the space requirements of a life science building.
The first part of the list includes generic spaces that are commonly found in many office buildings. Subsequent items on the list are incorporated to accommodate the life science element, ie the labs, specialist spaces and storage of gases etc.
- Social/communal spaces
- Café, collaboration zones, town hall, showcase and possible lecture halls
- Circulation spaces
- Corridors stairs, lifts and goods lift etc
- Utility spaces
- Non-research storage, plant rooms, risers, cleaning cupboards, WCs and showers etc.
- Office Space
- Write up research/review data/standard office space, meeting rooms and meeting pods etc
- Wet Labs
- Research space – microbiological cabinets, freezers, tissue culture rooms etc
- Dry Labs
- Similar to standard offices but more MEP – Data/Power
- Specialist spaces
- MRI, environmental rooms, technical or specialist/additional plant spaces etc.
The ratio and sizes of the dry lab, wet lab and specialist spaces are of course specific to the intended use of the building and the type of research and development planned.
The current life science hot spots in the UK are Oxford, Cambridge and, to a lesser extent, London. According to Savills, the ‘Oxford-Cambridge Innovation Arc’ leads the way in terms of venture capital fundraising[7]. However, both are restricted from a development perspective due to their historic nature and competing use for space. Despite this, wanting to reach its potential as a global tech and life sciences hub, Oxford City Council granted planning permission to build ‘Oxford North’ – a new £500m life sciences district set across 23 acres of green, open spaces that will offer 936,500 sq ft of lab and office space to support science, research and innovation. The district will rival the likes of Silicon Valley-style tech parks in the US and will see the creation of 480 new homes, small shops, bars and restaurants, a hotel and three new parks. More details on the project, on which G&T is providing Cost Management and Project Management services, can be found here.
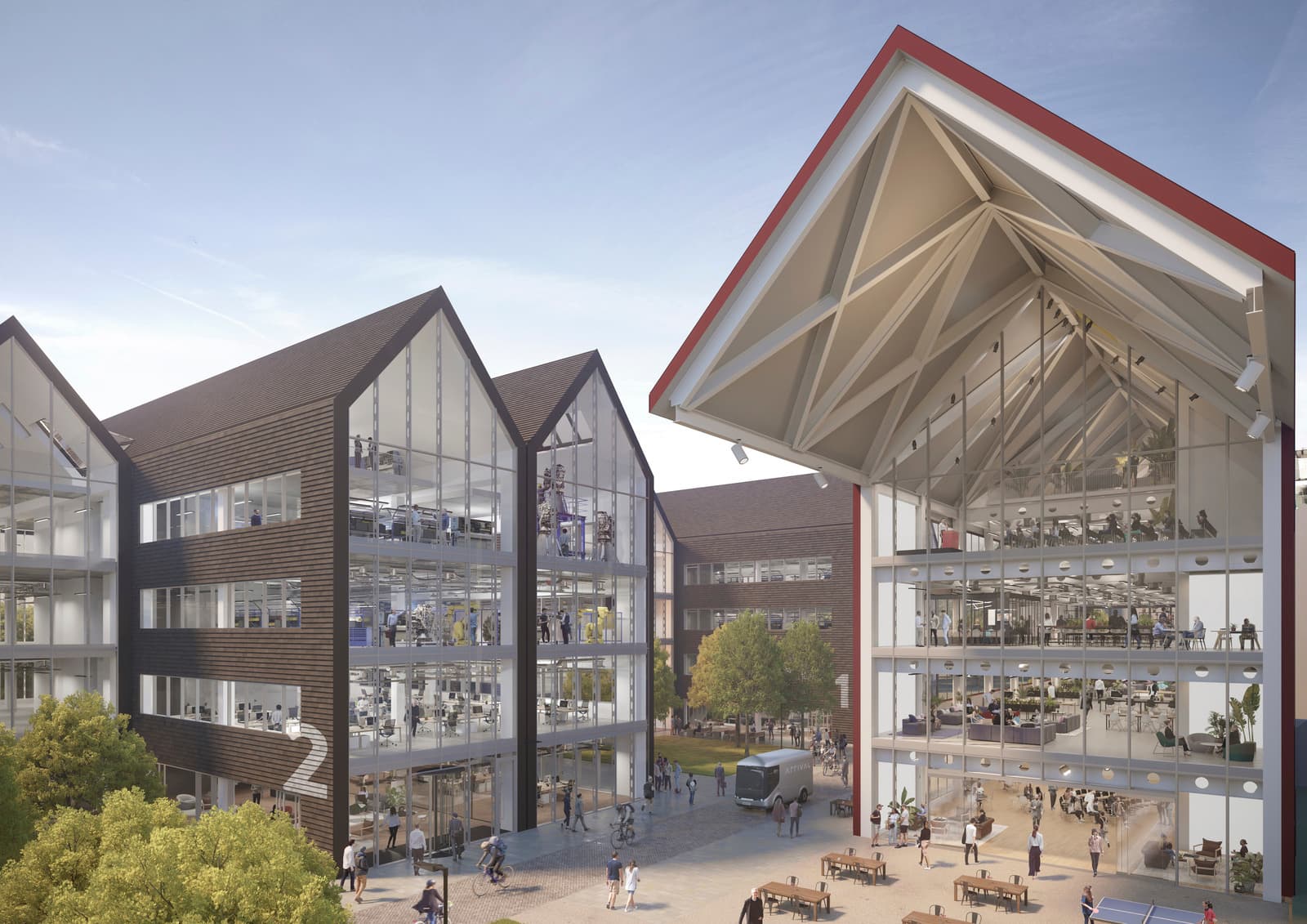
Oxford North - G&T is providing Cost and Project Management services - image courtesy of Fletcher Priest Architects
How are labs categorised?
There are a variety of ways in which laboratories are classified depending on their function:
- For wet laboratories where biohazards are in use, Biosafety Levels (BSL’s) are used
- For laboratories where potentially hazardous chemicals are used, Performance-Based Occupational Exposure Limits are used (PBOEL)
- For clean laboratories, these can be classified from the requirements for limiting particles in the air. Within Europe, this tends to follow the GxP grading system (Grades A - D), but can also be classified by the ISO system (ISO 1 – 9)
Wet labs researching biohazards are placed into four categories, or levels. Biosafety Levels (BSL) are used to identify the protective measures needed in a laboratory setting to protect workers, the environment, and the public. International BSL’s are defined by The U.S. Department of Health and Human Services, Public Health Emergency[8].
Biosafety categorisation starts at Level 1. BSL-1 requires no containment and poses minimal potential hazards to personnel with the least onerous requirements for labs and researching samples like E.Coli. The highest level of biosafety (BSL-4) requires facilities to provide maximum containment controls. Agents requiring BSL-4 facilities pose a high risk of life-threatening disease and are used for handling dangerous agents such as the Ebola virus.
Below is a high-level description of the four biosafety levels:
Biosafety Level 1 (BSL-1)
BSL-1 labs are used to study infectious agents or toxins not known to consistently cause disease in healthy adults. They follow basic safety procedures, called Standard Microbiological Practices and require no special equipment or design features. Standard engineering controls in BSL-1 laboratories include easily cleaned surfaces that are able to withstand the basic chemicals used in the laboratory.[9]
Biosafety Level 2 (BSL-2)
BSL-2 laboratories are used to study moderate-risk infectious agents or toxins that pose a risk to health if accidentally inhaled, swallowed, or exposed to the skin. Design requirements for BSL-2 laboratories include hand washing basins, eye washing stations in case of accidents and doors that close automatically and lock. BSL-2 labs must also have access to equipment that can decontaminate laboratory waste, including an incinerator, an autoclave and/or another method, depending on the biological risk assessment.[10]
Biosafety Level 3 (BSL-3)
BSL-3 laboratories are used to study infectious agents or toxins that may be transmitted through the air and cause potentially lethal infection through inhalation exposure. Researchers perform all experiments in biosafety cabinets that use carefully controlled air flow or sealed enclosures to prevent infection. BSL-3 laboratories are designed to be easily decontaminated. These laboratories must use controlled, or “directional,” air flow to ensure that air flows from non-laboratory areas (such as the hallway) into laboratory areas as an additional safety measure.[11]
Other engineered safety features include the use of two self-closing, or interlocked, doors, sealed windows and wall surfaces, and filtered ventilation systems. BSL-3 labs must also have access to equipment that can decontaminate laboratory waste, including an incinerator, an autoclave and/or another method, depending on the biological risk assessment.
Note – the US Centre for Disease Control and Prevention (CDC) recently outlined biosafety guidelines[12] stipulating that clinical laboratory and support staff that handle or process specimens associated with COVID-19. Those handling cultures of the SARS-CoV-2 virus 19 need to do so in a BSL-3 laboratory. Routine diagnostic testing procedures (refer to CDC for list of tests) can be handled in BSL-2 laboratory.
Biosafety Level 4 (BSL-4)
BSL-4 laboratories are used to study infectious agents or toxins that pose a high risk of aerosol-transmitted laboratory infections and life-threatening disease for which no vaccine or therapy is available. The laboratories incorporate all BSL-3 features and occupy safe, isolated zones within a larger building or may be housed in a separate, dedicated building. Access to BSL-4 laboratories is carefully controlled and requires significant training.
There are a limited number of BSL-4 facilities within the UK. They fall under the control of health authorities and have strict requirements for operation, including a minimum two-person policy (no lone working), along with training for emergency extraction.
There are two types of BSL-4 laboratories:
- Cabinet laboratory – all work with infectious agents or toxins is done in a Class III Biosafety Cabinet with very carefully designed procedures to contain any potential contamination. In addition, the laboratory space is designed to also prevent contamination of other spaces
- Suit laboratory – laboratory personnel are required to wear full-body, air-supplied suits, which are the most sophisticated type of personal protective equipment. All personnel shower before exiting the laboratory and go through a series of procedures designed to fully decontaminate them before leaving
The engineering controls required are different for BSL-4 cabinet and suit laboratories, but for either type, the controls are extensive and are supplemented by carefully designed procedures and practices.[13]
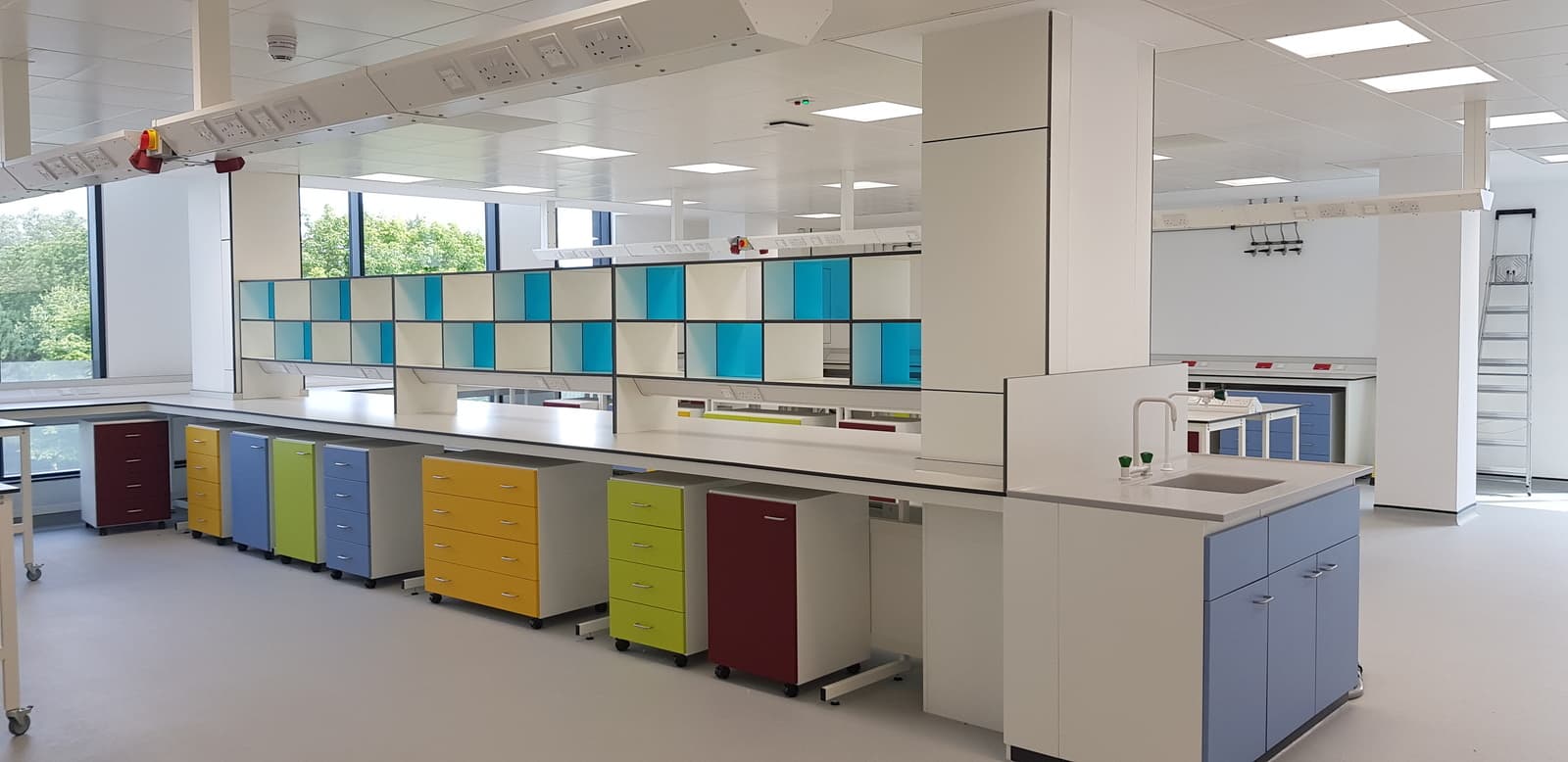
Ipsen, Milton Park - G&T provided Cost Management, Project Management and Contract Administration services
The basic characteristics of a life science building
It’s important to understand what “special” characteristics are required from a life science building, over and above that of a standard building, in order to accommodate the “labs”.
The non-exhaustive list below indicates some of the characteristics applicable to all biosafety levels and lab types. However, for BSL-3 and 4, the requirements become more onerous and specific depending on the type of lab and the research being undertaken within it.
- Stiff structure to achieve required vibration control (for lab areas)
- Enhanced capacity/loading of structures for equipment
- Consideration of flat slab design to facilitate horizontal air distribution
- Additional power/air/filtration/extraction (wet lab with 6+ air changes per hour, small power double British Council for Offices (BCO) standards, dry labs even quadruple BCO standards)
- Enhanced service zones (vertically and horizontally) including provision for future expansion
- Soft spots to allow future fume hoods to be installed (or provision for)
- Ability to expand the service yard to allow for receipt and dispatch of controlled chemicals
- Specialist fume/extraction or high efficiency particulate air (HEPA) filtration and recirculation
- High floor heights (ideally a minimum of 4 to 4.5m slab-to-slab)
- Additional lifts and service lifts with access to service yards
- Enhanced security provisions including tenant to tenant and intellectual property security
- Backup power generators and substantial uninterrupted power supply (UPS)
- Specialist media (gas and liquid) supplies from central or local supply
- Plant space for segregation of landlord and tenant(s) plant
- Building utilities (power, water and sewage) to be increased
- Expansion plant space for future additional power, generators, specialist gas supplies, filtration etc
A specialist designer should be engaged to develop the design criteria and building characteristics required for a specific life sciences project development.
New build or conversion?
A new build project is ideal for a life science development. It allows the building characteristics listed above to be embedded within the design from RIBA Stage 0. It also means that all of the aforementioned “spaces” can be designed in to the building, making it easier to plan the correct adjacencies and massing to create an efficient design that can optimise the use of the building.
Conversions are possible but are more feasible on BSL-1 and BSL-2 lab projects. The specific needs, requirements and specialist spaces required in BSL-3 and BSL-4 labs mean that conversions become substantially more onerous, increasingly difficult and cost prohibitive to achieve. As such, virtually all BSL-3 and BSL-4 labs are located within new, purpose-built buildings or developments.
The level of work, effort, time and cost to convert an existing building into a life science building is dependent on the design of the existing building, its characteristics and what the requirements are of the converted life science building and its associated labs and specialist areas. When considering whether an existing building can be converted or adapted into a life science building, areas to review and consider should be based on the above list of building characteristics that are ultimately required.
Focusing on the characteristics that are more difficult (or indeed impossible) to modify is a good starting point when determining whether an existing building is suitable for a life science conversion. For example, structural frame heights between floors (which ideally need to be 4–4.5m) should be a key consideration, as is the structural frame spacing as this is complex to modify. You also need to consider the availability of space for the additional MEP and specialist fume/extraction, ie is there space and loading capacity on the roof for additional plant and equipment rather than inside the building? Also consider the type and condition of the existing façade/envelope. As labs require strict thermal controls and conditions, replacing a façade can be a complex, time consuming and expensive process.
The building’s base infrastructure, ie power, water and sewage, is another key consideration as these will need to be increased from that of a non-life science building. Ask whether it’s possible or practical to increase the incoming power from the local network? Do the local sewers have capacity for additional flows?
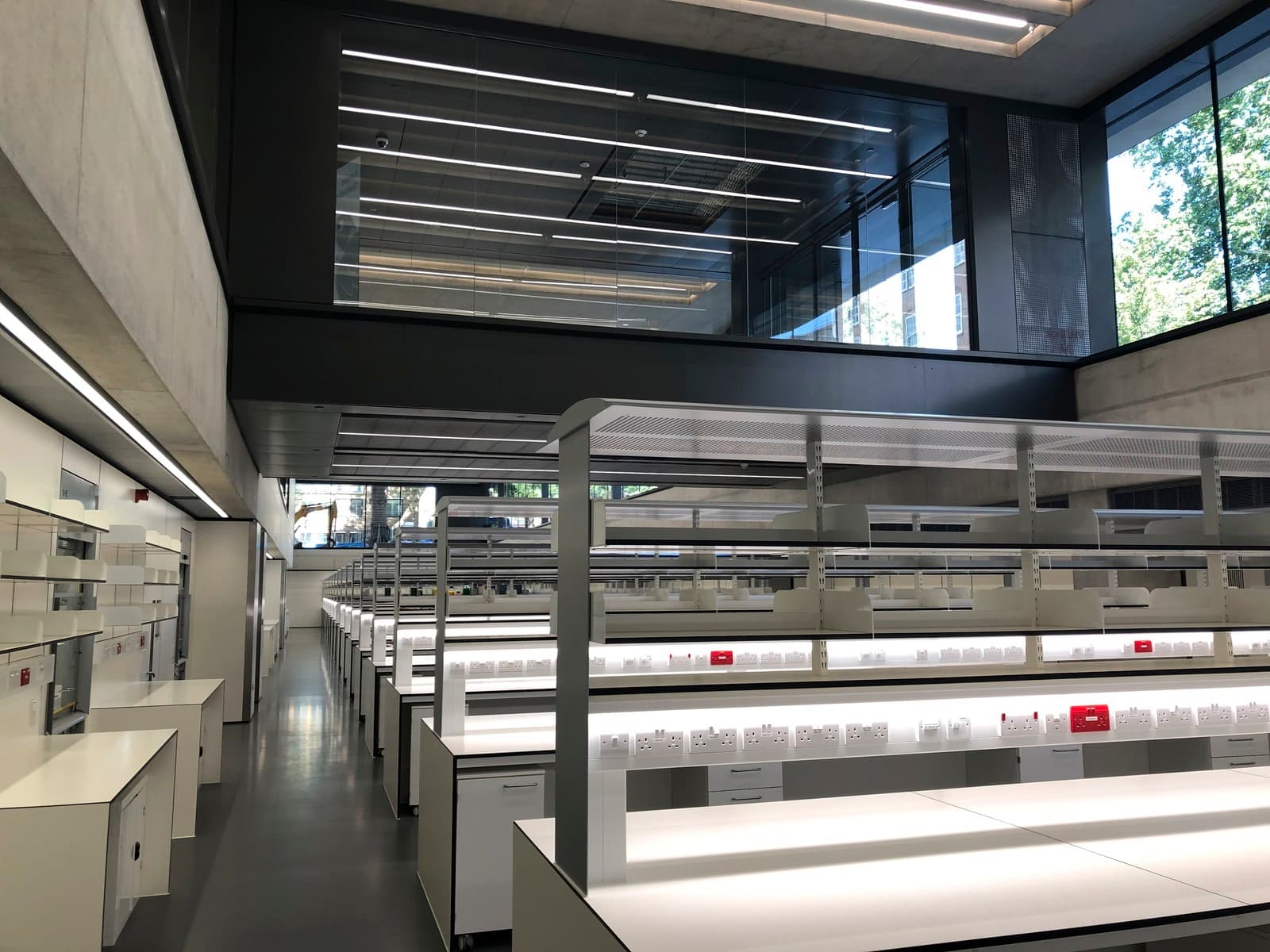
Zayed Centre for Research into Rare Disease - G&T provided Cost and Project Management services
Future-proof a new “office” development for “life sciences”?
With additional capital investment, it is possible and practical to future-proof a new office development to allow for future flexibility to be fit-out as a life science building. Again, this is more applicable to BSL-1 and BSL-2 labs.
As previously noted, virtually all BSL-3 and BSL-4 labs, and the buildings housing said labs, are purpose-built. It is not practical to future-proof a new office development for these biosafety levels. However, for BSL-1 and BSL-2 the key characteristics to be embedded in the design from day 1 are listed below. This is followed by a list of other elements that could form part of a life science day 2 fit-out:
Day 1 (base build):
- Stiff structure to achieve required vibration control (for labs and specialist areas)
- Consideration of flat slab structures to assist horizontal service distribution and reduce slab-to-slab height
- Enhanced capacity/loading of structures for equipment
- Grid layout to be positioned to provide the maximum flexibility for laboratories
- High floor heights (ideally min 4–4.5m slab-to-slab)
- Enhanced service zones (vertically and horizontally), including provision to expand these
- Soft spots to allow future fume hoods to be installed (or provision for)
- Enhanced security provisions (more can be added as required at day 2)
- Additional lifts and service lifts with access to service yards (additional lifts could be added on day 2, however shafts to be provided at day 1)
- Services and primary plant strategy to facilitate leasing/tenant strategy and associated marketing flexibility – single or multi-tenant facility
- Ability to expand the service yard to allow for receipt and dispatch of controlled chemicals
- Expansion plant space for future additional power, generators, specialist gas supplies, filtration etc
- Capacity to increase the building’s utilities (power, water and sewage)
Day 2 (life science fit-out):
- Additional power/air/filtration/extraction
- Specialist fume/extraction or HEPA filtration and recirculation
- Backup power generators and substantial UPS
- Specialist media (gas & liquid) supplies from central or local supply point
- Additional lifts (if not installed at day 1)
- Additional security requirements
- Specific lab fit-out
- Specialist spaces fit-out
The key for future-proofing buildings for eventual use by the life sciences sector is designing and building in the flexibility for the day 2 fit-out. However, the more flexible the building, the more costly it will be and the more space will need to be allocated for “future use”. Conversely, the greater the flexibility that can be designed and built in, the easier it will be to efficiently convert and fit-out the building for future life science tenants and, in turn, make the day 2 conversion less costly.
Conclusion
The vibrant health of the growing sector (which was worth more than £81bn in the UK and employed over 250,000 people in 2019[14]) and the fact that it’s a key industry that can take advantage of some of the opportunities arising as a result of Brexit and the global pandemic, has encouraged a number of life science businesses to manufacture more locally to avoid disrupted supply chains.
According to a report[15] from Savills, Perkins&Will and Blackstock Consulting, between 2016 and 2020, an average of £247m per year was pumped into life sciences real estate in the UK. However, the report forecasts that investment will reach a new high in 2021, predicting that investment could more than double to £550m. If the current pace of investment growth continues, by 2025 investment into the UK life sciences property market could reach up to £2bn. With this increased investment will come the need for additional research and lab workspace. However, as has been established, the short-term pipeline for commercial lab space is lacking with very little new space coming through in the next couple of years.
The shortage of lab space is driving developers and operators to consider converting existing commercial office space to life sciences buildings – a potentially faster and more efficient solution than building new facilities. Shortages are also prompting some stakeholders to consider how they can future-proof standard commercial office developments to allow for future flexibility in converting or adapting the space for life sciences use.
If you would like to learn more about how G&T can help deliver your life sciences building project - whether it be a new, purpose-built facility, a conversion or adaptation of an existing building, or even future-proofing your new office project for potential life sciences use in the future - please contact your usual Partner at G&T.
Please note: The information provided and views expressed in this article are based on G&T’s direct experience in the Life Sciences sector. We suggest that you seek out expert design advice before proceeding on your project.
[2] Professor Sir John Bell – Life Science Industrial Strategy
[3] Life Science competitiveness Indicators 2020, Office for Life Sciences
[5] https://www.crbgroup.com/insights/lab-design
[6] Ibid
[8] U.S. Department of Health and Human Services, Public Health Emergency
[9] U.S. Department of Health and Human Services, Public Health Emergency
[10] Ibid
[11] Ibid
[12] https://www.cdc.gov/coronavirus/2019-ncov/lab/lab-biosafety-guidelines.html
[13] U.S. Department of Health and Human Services, Public Health Emergency
[14] Life Science competitiveness Indicators 2020, Office for Life Sciences