Q4 2023
Input Costs
Key inflationary and deflationary pressures
Despite the UK construction sector seeing a significant easing in input cost inflation this year, some elements of inflation continue to work through the system.
Higher interest rates, softer energy and material prices, combined with a normalisation of demand conditions and certain regulatory hurdles have conspired to slow the overall rate of tender price inflation in 2023. Labour (which can account for around 40% of the cost of a commercial office scheme) has been the clear driver of inflation this year. The BCIS’ cost indices suggests that labour costs will rise by 6.8% in 2023, more than offsetting softer material price inflation and falling plant costs.
With UK consumer price inflation set to fall back to around 2.7% in 2024 (based on an average of independent forecasts), this should theoretically take some pressure off labour cost inflation. The dynamic interaction between prices and wages is that if workers see and expect prices to rise, they demand higher wages so that their real (inflation adjusted) wages are constant. With raw and building materials generally levelling off (and in some cases, falling significantly), on the current trajectory, construction input inflation should return to more typical, long-term average levels next year. This is demonstrated in the BCIS’ General Building Cost Index, which after rising 8.7% in 2022, is set to fall towards a more typical annual rate of 3.2% in both 2023 and 2024.
However, softer input cost inflation is unlikely to fully compensate for higher interest rate costs. New order growth will likely remain weak until there are clearer signs that borrowing costs are falling and clients are more confident about the direction of travel across the wider economy. Once there is greater clarity regarding these two market-influencing factors, recently stalled projects could be green-lit and a wave new work unleashed.
Material Costs
The supply costs for many of the major material elements in the UK construction sector have come off considerably this year. Structural steel, rebar and imported timber have all experienced strong deflationary trends since mid-2022, resulting in the BCIS’ ‘All Work’ material price index (a basket of goods that tracks price movements for construction materials) to experience its first annual contraction since September 2020.
Although still elevated by historical measures, according to July’s data, material prices were on average 4% lower than they were one year ago. The welcome and positive trend has been led by falling wholesale energy prices, oversupply issues at stockists (following a reversal of the supply-side squeeze during the pandemic) and normalising demand.
However, prices for some product categories (eg insulating materials, concrete/cement and electrical materials) are still rising.
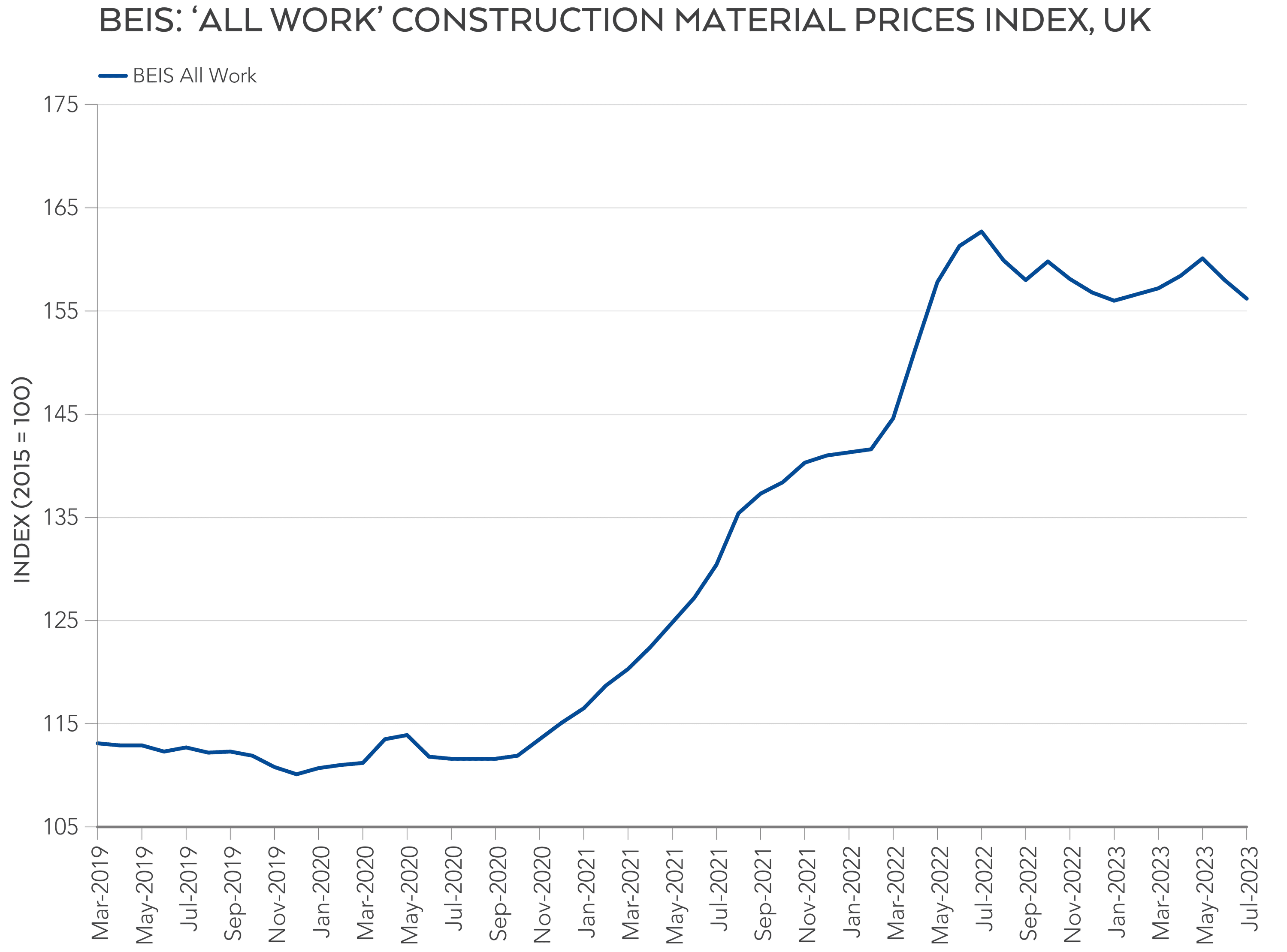
As one of the key elements of the construction industry’s purchase of inputs, falling material prices is positive news for overall construction costs, but there is still a wide range of inflationary rates across the basket of tracked materials.
Ready-mixed concrete is a stand-out example, with prices having increased by more than 20% in the year to July 2023. Upward price pressure in this instance stems from the lingering effects of historically high energy costs, the rising cost of aggregates and higher labour and equipment costs required for batching, mixing and transportation to site. It is expected that lower wholesale energy prices will eventually filter through the supply chain, putting further downward pressure on prices. However, supporting prices will be higher demand for low-carbon variants of concrete which, due to the additional steps and materials involved in its production, has a cost premium to standard cement.
Meanwhile, the cost of heavy materials such as steel, bricks and timber have fallen in response to the slowdown in the new-build sector (in contrast to the buoyancy of refurbishment and energy-efficiency retrofit work). Manufacturers have experienced a significant drop in sales for products that are typically used at the earlier stages of construction. Steel manufacturers like British Steel have tried to stymie the trend of falling prices by announcing price increases (eg British Steel’s £30/t hike on structural sections in July) but these increases have generally not stuck. Stocks remain high compared to current demand, maintaining downward pressure on prices for the time being. However, once the current oversupply issues have eased, prices may start to rise once again.
With material price inflation becoming less volatile and more predictable, price fixing has become less of an issue and some contractors are showing increased willingness to fix for longer periods.
The ongoing war in Ukraine and, to a certain extent, the recent conflict in the Middle East, will continue to impact manufacturers of energy intensive products. With the UK’s energy supply far from secure, many have therefore hedged their energy contracts into 2024. However, by insulating themselves against global energy shocks, the cost of manufacturing these products will remain elevated compared to the levels seen before the outbreak of the war in Ukraine. A weaker pound is another factor that is likely to maintain price pressure on imported construction materials and components. Sterling’s current weakness is undeniably a concern, not least because international commodities priced in dollars – including oil – place additional cost pressures on UK businesses and consumers at a time of already high inflation.
Overall, the levelling off in material prices should be seen as a positive. Manufacturing input costs and factory gate prices have fallen over the past year and, although it may take time, softening production costs should flow into the wider economy. However, there are a variety of factors that could disrupt the current trajectory, ranging from further energy price spikes to changing demand conditions in China.
Labour
Labour supply issues continue to be a major challenge for the construction industry. Although the industry’s labour challenges may be tempered in the short-term by slowing new order growth and softer demand, demographic and structural issues will continue to put upward pressure on wages in the longer-term.
In the currently tight labour market, availability issues are intersecting with cost-of-living pressures, pushing earnings in the sector higher. According to ONS data, average weekly earnings in UK construction were 4.9% higher in July 2023 compared to a year ago (on a three-month average basis). This far exceeds the long-term average annual growth trend of 3.1%. However, as the ONS data captures all types of roles within the industry, this is likely to mask larger rises for certain specialist trades working on site.
For example, employers and unions on the Construction Industry Joint Council (CIJC) have concluded their negotiations and agreed an 8% rise in the general operative rate for site workers from 10th July 2023. The CIJC also agreed a two-stage increase for all other rates, amounting to a compound rise of 7.59%. Approximately 500,000 workers are affected by the agreement, which pushes their annual wage growth above the current rate of inflation in the wider economy (which was 6.7% in the 12 months to August 2023).
Rising labour costs are essentially a consequence of demand exceeding supply. Shortages in recent years have been exacerbated by strong workloads, the impact of Brexit on European labour supply and growing working-age inactivity rates. Other dynamics pushing wages higher include resource poaching and staff retention costs. In light of these pressures, labour remains on track to be the main input cost driver in 2023 and into 2024.
Estimates by the Construction Industry Training Board (CITB) suggest that the UK construction sector will need an additional 225,000 workers by 2027 to meet projected domestic demand. While this estimate might not have factored in the current drop in demand for construction work, the task of acquiring such a substantial workforce is bound to be challenging.
The number of vacancies in UK construction has dropped in recent months, falling from their 20-year record high of almost 50,000 job openings in the middle of 2022. Construction vacancies in the June-August 2023 period of this year fell to 37,000, but this is still well above the 10-year average for vacancies (c.28,000). Falling vacancies have almost certainly been a consequence of easing construction output growth and uncertainly over future workloads and pipelines.
Despite an easing in the number of advertised vacancies, sourcing for several roles (professional and site-based) remains a challenge. While the Government recently accepted recommendations from the Migration Advisory Committee to add additional roles to the ‘shortage occupation list’ (including bricklayers and masons, roofers, carpenters and joiners as well as plasterers), contractors continue to report difficulties recruiting skilled labour for many of these occupations.
On-costs
In ‘percentage-of-total-project-cost’ terms, around 30-40% of those surveyed reported that project preliminaries costs had risen in Q3 2023. The rest noted no change over the period. Those that did report increasing preliminaries costs explained this was being driven by higher wages for staff and skilled management. Rising plant operational costs were also flagged as a reason for higher preliminaries.
Conversely, overheads and profit (OH&P) remained broadly consistent, with the majority of those surveyed (between 50-60%, depending on the project value) suggesting there has been no movement over the past three months. In one instance, a respondent anecdotally noted that on one project, the same contractor placed two bids on the project 12 months apart. While their preliminaries allocation has increased, OH&P remained unchanged from the original bid.
Over the next 12 months, many commentators suspect contractors will have to compete more heavily on price and will therefore lower their returns and controllable costs to secure work. Increased levels of tendering competitiveness will naturally drive a review but with the current labour pressures, preliminaries costs are unlikely to come down significantly.