In order for the UK to meet its climate change targets by 2050, all new buildings must operate at net zero by 2030 which, according to the UKGBC means that all new buildings will have to be designed to meet the target of net zero operational energy by 2025. In the second in our series of articles on low carbon buildings, we look at the UKGBC’s “Building the Case for Net Zero” report and ask if net zero carbon really is obtainable in construction by 2050.
In 2020, the world’s first building to be verified as net zero carbon for construction was built. Verified using the UKGBC’s Net Zero Carbon Buildings Framework, the specifications of the Essex-based warehouse (called ‘Magnitude’) maximised the efficiency and sustainability of the materials used which significantly lowered embodied carbon levels. Material manufacturers were required to provide a breakdown of their products, stating its origin, embodied carbon and its ability to be re-used/re-cycled. The milestone development may help pave the way for further net zero carbon developments.
In fact Landsec, a FTSE-100 property developer, is progressing plans to build what aims to be the UK’s first net zero-carbon commercial building. Using innovative building techniques, experts have said that The Forge embodies what the future of construction will be.
As 40% of the UK’s carbon emissions are attributable to the built environment, the sector needs to be pursuing more aggressive rates of decarbonisation. But there are currently no UK commercial buildings which are considered net zero, in both construction and operation according to the UK Green Building Council’s (UKGBC) net zero carbon buildings framework.
The Forge, previously known as 105 Sumner St, is a 139,000/140,000 sq ft office development in LB Southwark which aims to change this. It aspires to be the first commercial building to be both constructed and operated in line with UKGBC’s framework and associated energy performance targets. It is also the first major commercial building to be built using a platform approach to design for manufacture and assembly.
How do you build a net zero carbon building?
Developing a net zero carbon building means addressing scope 3 emissions. These are the emissions that are a consequence of a company’s actions, but which occur at sources that the company does not own or control directly.
Construction activities account for a large part of the construction development industry’s scope 3 emissions. These include: supply-chain emissions that arise from the extraction of resources; manufacturing products; transporting materials; and assembling the building. These are often referred to as ‘embodied carbon’.
The Forge will be one of the most innovative construction sites in the capital. Landsec, along with tech-led design practice Bryden Wood, and design development and prototyping company Easi-Space, have been awarded funding from Innovate UK, the UK’s innovation agency, to deliver what will be the world’s first ever office building using a platform-led approach to design and construction.
What is a platform-led approach and what are the benefits?
The platform system, known as P-DfMA (Platform for Design, Manufacture and Assembly), consists of a set of components that can be combined to produce highly customised structures. This means that different kinds of spaces can be built with just a single ‘kit of parts’. This method has been identified by the Government as key to the transformation of the construction sector.
A research and development trial prototype of this approach, led by Landsec, Bryden Wood and Easi-Space, had positive results:
- construction productivity improved by 55%, when compared to productivity on a traditional construction site
- the time it took to install the building was reduced by 30%, when compared to using traditional construction techniques
- the final build achieved 33% cost savings, when compared to traditional construction techniques
The result is a structure that uses less material, creates less waste and has an almost 20% reduction in embodied carbon compared to a traditional build. Further have since been made through careful specifications, including high levels of recycled content and cement replacement in the main building materials.
“With its innovative platform technique and ‘kit of parts’ approach [The Forge] embodies what the future of construction will be,” says Sam Stacey, Challenge Director for the Transforming Construction Challenge at UK Research and Innovation. “Such approaches are essential to the transformation of the construction sector.”
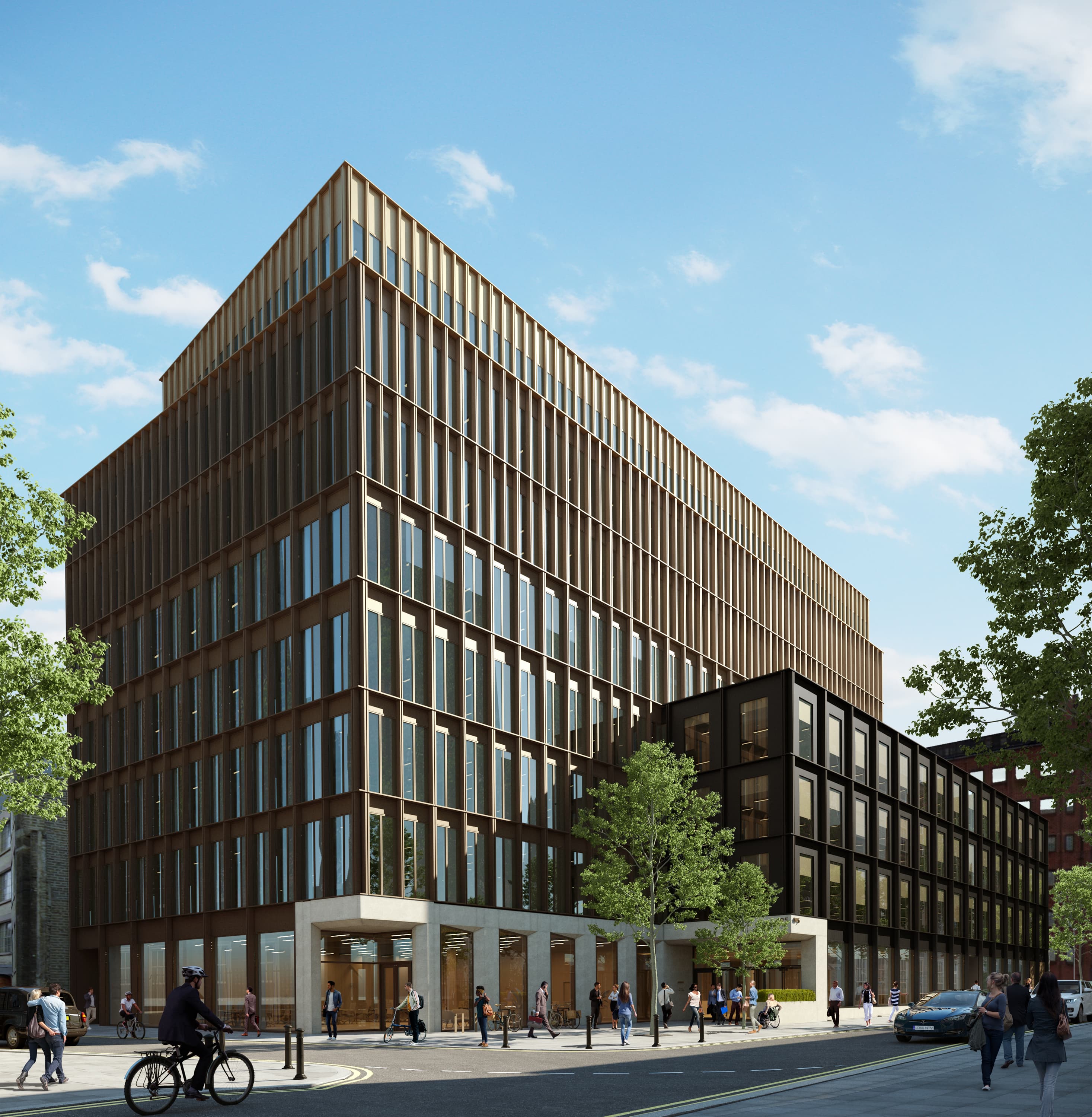
How do you operate a net zero building?
Embodied carbon is only a part of the net zero story; operational energy efficiency is also fundamental to achieving a truly net zero carbon building.
At The Forge, passive design techniques were used to reduce the energy demand of the building before adopting the use of highly efficient air source heat pumps (ASHP) to provide heating and cooling. Once in operation, these will be run on 100% renewable electricity tariff. An array of photovoltaic panels are provided at roof level which will offset the annual emergency generator diesel fuel required for ongoing maintenance requirements.
In order to tackle the ‘performance gap’ the building was modelled using the Design for Performance approach. This allows the team to predict actual energy use and to model different off-axis scenarios to stress test the system and fine-tune it accordingly, increasing its efficiency further.
Julie Hirigoyen, Chief Executive at UKGBC, also praised the development:
“The Forge is a ground-breaking development and testament to Landsec’s desire to tackle the climate crisis head on. Developers, construction firms, architects and occupiers must start working together at scale to deliver buildings like this that minimise whole life carbon and contribute to meaningful progress in the battle against climate change.”
Lessons for the built environment sector
In 2016 Landsec became the first property company in the world to adopt a science-based target to tackle emissions and has since launched a five-step plan to become a net zero carbon business by 2030 (20 years ahead of the UK Government’s legally binding target). Using science-based targets will see Landsec reduce absolute carbon emissions by 70% from a 2014 baseline over the next ten years but investments will have to be made to offset the residual 30%.
And once The Forge is completed, all of Landsec’s future developments will be built to – and operate in line with – UKGBC’s net zero carbon buildings framework. The hope for the wider built environment sector is that The Forge will act as a ‘demonstrator project’ for other developments, and help make the business case for other developers to commit to more net zero buildings.
Building the Case for Net Zero
Whilst developments like these prove that net-zero carbon in construction is possible now (albeit with some offsetting), meeting these targets is currently far from easy and such projects tend to see significant cost premiums over more traditional/conventional builds.
A new report from the UKGBC called ‘Building the Case for Net Zero’[1] presents the findings of a feasibility study illustrating how buildings can be designed to reach net zero performance targets and the impact this has on cost. The study looked at two real-life buildings at concept design stage (one residential block and one office building) and produced two further iterations for each - one ‘intermediate’ scenario looking to meet the 2025 net zero performance targets and one ‘stretch’ scenario with the more ambitious 2030 carbon targets in mind.
This particular study used net zero performance targets from the UKGBC[2], the London Energy Transformation Initiative (LETI)[3] and RIBA[4] for both embodied carbon and operational energy. It’s worth noting that the UKGBC study did not use RIBA’s targets for embodied carbon because RIBA’s targets are for whole life embodied carbon, whereas the LETI targets are until practical completion only (aligned with UKGBC’s 1.1 Net zero carbon – construction). The performance targets are summarised below:
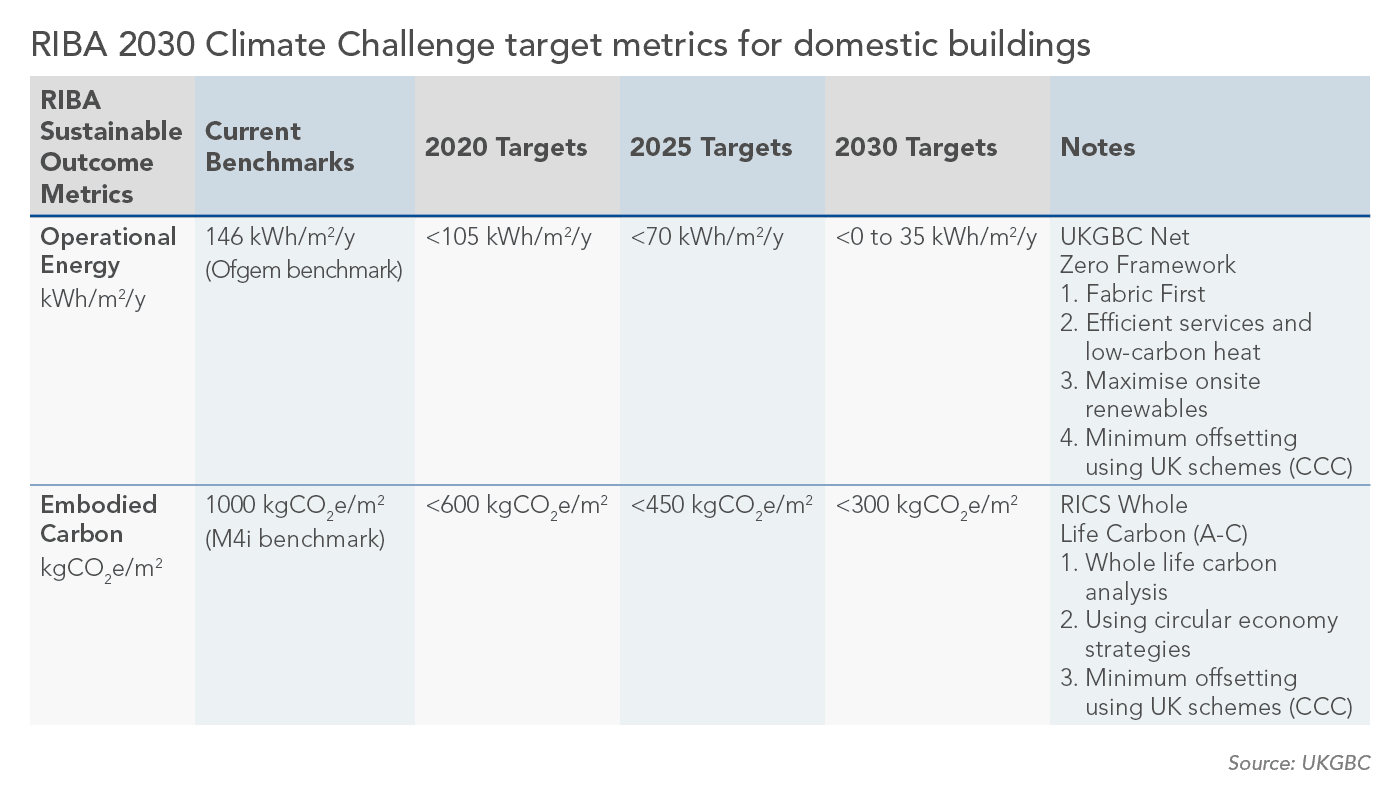
The ‘Baseline’ or original office design (which represents business as usual levels of performance) is shown against the ‘Intermediate’ and ‘Stretch’ scenarios in the graphs below.
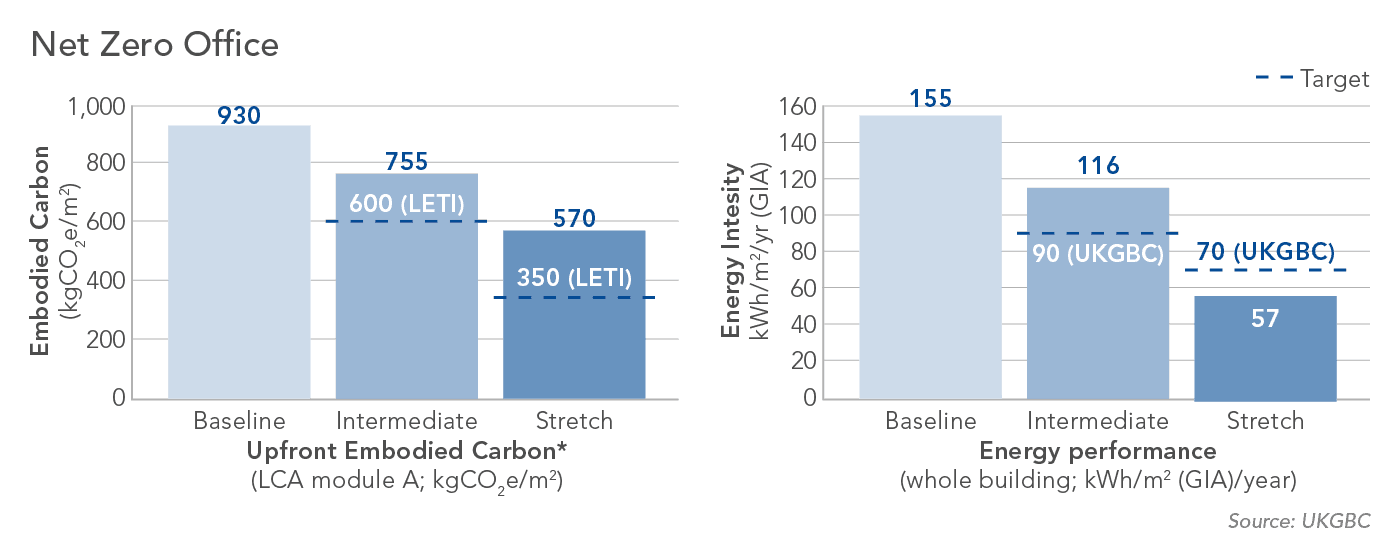
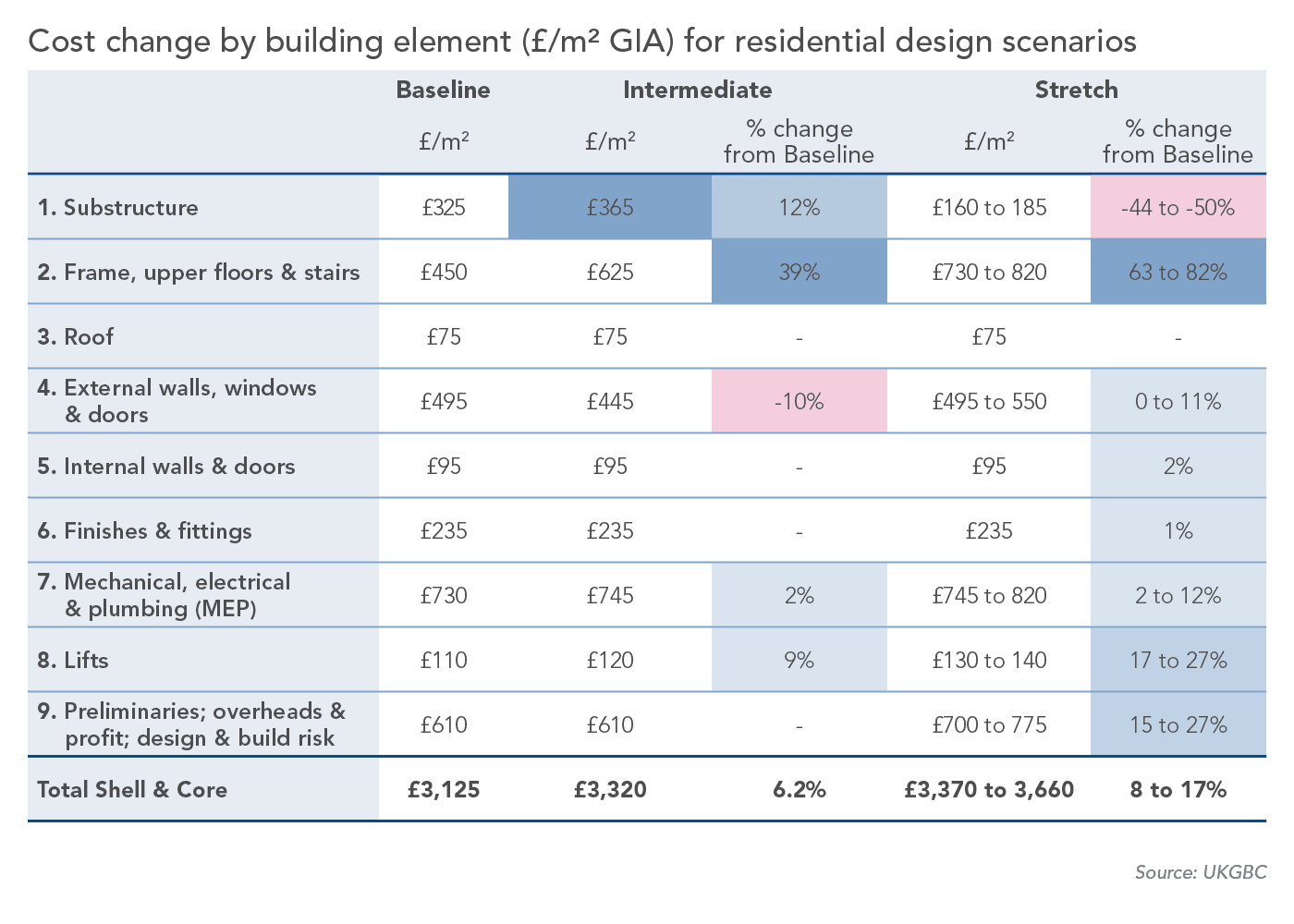
The baseline design for the office scheme was a BCO Grade A, 16-storey city office building on an urban infill site with strong environmental aims. The project team’s brief was to deliver the same building that had achieved planning approval (ie same overall volume, external massing, site conditions), with free reign to alter all other design parameters (eg structure, HVAC system, tenant requirements etc) to achieve, or get as close to achieving, the relevant net zero performance targets for 2025 and 2030.
The graph above shows that the embodied carbon performance targets (published by LETI) were not achieved under the intermediate (2025) and stretch (2030) scenarios for the office scheme. The intermediate scenario for energy performance (ie operational carbon) was also unable to meet the UKGBC 2025 carbon target. However, the stretch target for 2030 was met as a result of some key design changes to the fit-out to drive down energy usage. The key change being adopting off-site cloud computing and limiting the on-site server room usage to 0.5W/m². This effectively shifted the associated energy usage and carbon emissions from one building (the office) to another (data centre), outside the study boundary.
The residential building, as shown below, performed a little better in terms of meeting the performance targets:
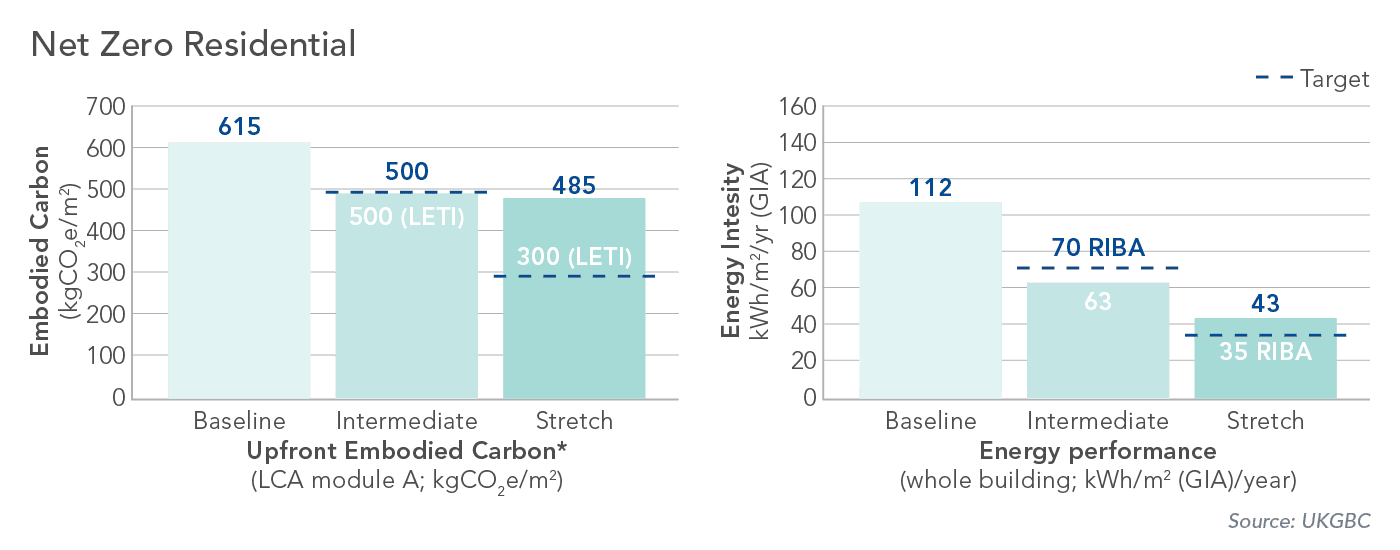
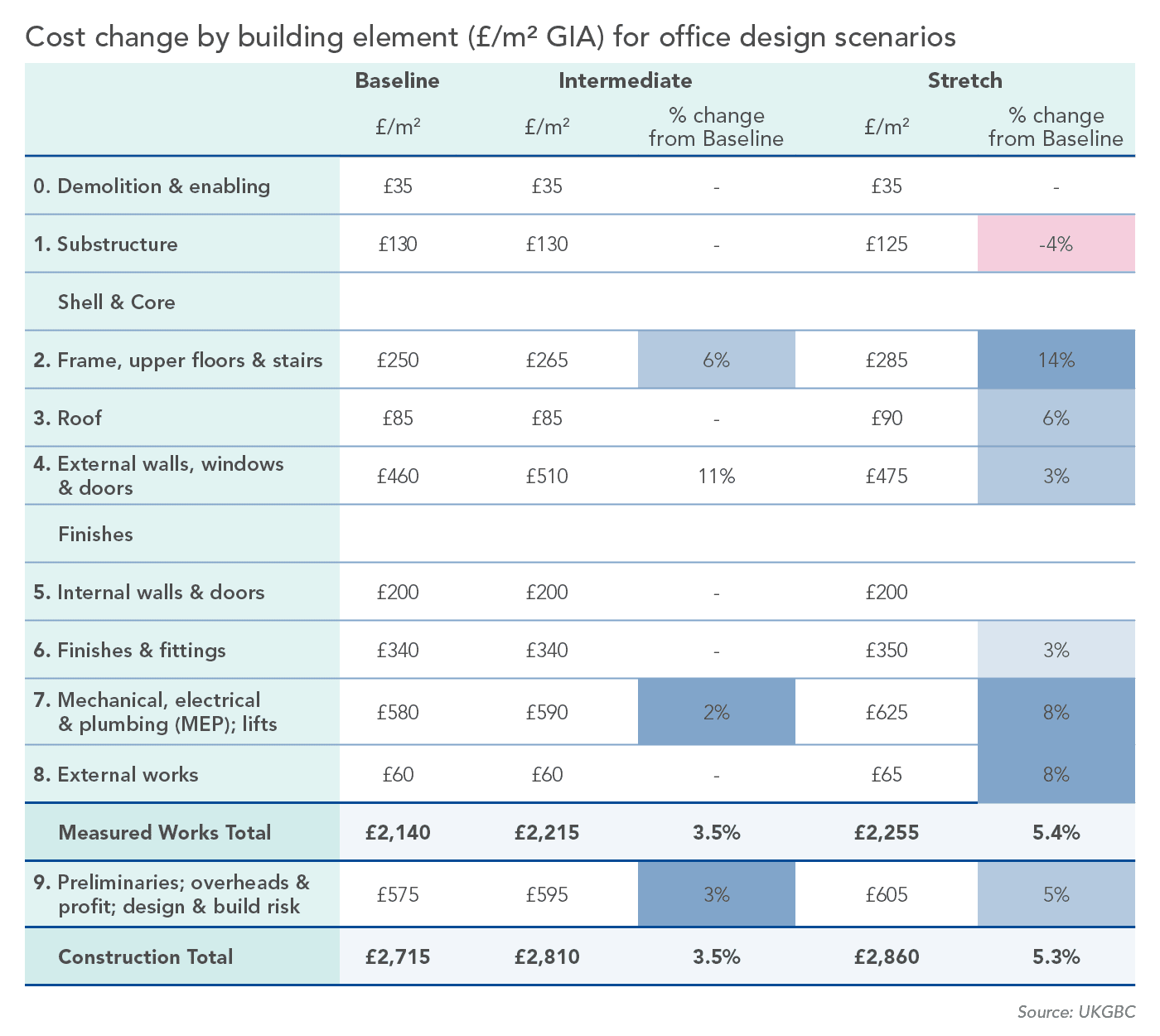
For embodied carbon, the residential building was able to meet the intermediate LETI target but not the stretch target. For operational energy performance the intermediate RIBA target was also met but the design changes made to the building weren’t able to hit the 2030 stretch target.
To fully meet these targets, the report noted that radical changes to the original building design would have been required. In terms of the effect on cost, the study found that for the office there was a 6.2% uplift in cost when trying to reach the intermediate 2025 carbon reduction target and an 8-17% uplift for the advanced 2030 goal when compared to the baseline scenarios. The residential building, however, only saw a 3.5% and 5.3% uplift respectively.
It is clear that the net zero targets for 2030 are substantially more demanding and the market is not quite yet geared up to deliver these targets at scale. The capital cost uplift for the intermediate scenarios is more feasible, especially given that these extra costs may be offset by the value benefits, eg increased rental premiums, lower tenancy void periods, lower offsetting costs and lower operating/lifecycle costs. However, these value benefits are suggestive and have to be balanced against real, tangible losses in floor space, basement floors, roof amenities etc. These losses may make some schemes unviable.
It was also noted that the cost premium could be tackled by Government intervention. Guaranteeing certainty with a long-term and consistent regulatory pathway that increasingly tightens standards would motivate the supply chain to invest and innovate. Given that these intermediate targets will be necessary to meet the ultimate 2050 net zero goal, the Government will be strongly incentivised to tighten these regulatory standards.
Embodied Carbon in the UKGBC Report
The amount of embodied carbon (as measured in kilograms of carbon emitted per square metre - kgCO2e/m²) that is emitted during the non-operational phase of a project will inevitably vary by size and building type. However, for new buildings, the embodied emissions from construction can account for up to half of the carbon impacts associated with the building over its lifecycle[5].
Based on the UKGBC feasibility study referenced above, it appears that the embodied carbon reduction targets will be more difficult to achieve than the operational targets. The RIBA 2030 Climate Challenge document recognises this and suggests maximising the use of existing assets, prioritising retrofitting existing buildings where possible in order to reduce embodied carbon emissions. Where not possible, it suggests that new buildings use low-carbon healthy materials that are responsibly and ethically sourced and minimise resource consumption[6].
Embodied carbon can be lowered significantly in the product and construction stages. The UKGBC study[7] found that during the fit-out process, embodied carbon savings can be made by reducing, or removing entirely, any excessive material finishes (known as ‘dematerialisation’). For example, an embodied carbon saving of 14% was made on the intermediate office scenario compared to the baseline design by simply not installing a suspended aluminium ceiling due to its regular need for replacement during the life of a building.
Substantial embodied carbon savings were also found by replacing steel and concrete in the structure – two of the most carbon intensive materials used in buildings. Steel is responsible for approximately 7%[8] of global carbon emissions and around concrete 7-9%[9]. Using a full timber structure (ie glue laminated timber frame and cross-laminated timber floors) and removing the concrete basement in the office stretch design reduced total upfront or embodied carbon by 39% compared to the baseline. Using a structural timber frame also helped to reduce the weight of the building which led to smaller foundations. However, it’s important to note that using the larger-sized columns and beams does affect the building volume and therefore its final value.
For the residential building, the UKGBC study found that while low carbon concrete and post-tensioned concrete slabs helped to reduce carbon from fully concrete structures, using a timber frame (as was done in the 2030 stretch design scenario) achieved the most significant carbon reductions. There was a 74% reduction of the structural elements compared to the baseline design, representing a fall from 273 to 70kgCO2e/m². Again, using timber did result in an increased structural zone which meant that two floors had to be removed to maintain the building’s height. The loss of units would inevitably impact the final value of the building.
Despite the reduction of embodied carbon from the structural elements, the stretch design did still not meet the overall LETI 2030 embodied carbon target. Reaching this target is extremely challenging, especially when sequestration (the long-term capture and storage of atmospheric carbon) from timber is not included under this particular target.
At G&T, our recent experience on a 14-storey, 135,000 sq ft (GIA) office scheme based in Manchester revealed that even hitting the more achievable 2025 embodied carbon targets proved to be very difficult.
The design started with a timber frame and cross laminated timber (CLT) floors and core. The envelope included limestone and the scheme was designed to use a mixed-mode ventilation system (which involves opening windows as well as mechanical ventilation). Timber frames don’t work well over a certain height due to stability and fire risk issues, and also because of the increased number of timber columns that are required within the floorplates. As a result, the design was changed to use recycled steel, CLT floors and a concrete core. The concrete used a special aggregate which had good carbon credentials.
Overall, it was very challenging to strike a balance between the design, achieving the embodied carbon targets and ensuring the building was economical. The scheme ended up being considerably more expensive than a traditional design and significantly higher than the 6.2% uplift in the UKGBC’s intermediate (2025) office scenario. It should be noted, however, that the cost premium might also be a result of other factors.
While the scheme had initially set out to achieve the 2030 embodied carbon target, it will in fact struggle to hit the 2025 embodied carbon target.
How we manufacture and install materials and systems will play a big part in whether we achieve net zero carbon in construction. Much of the industry is still unfamiliar with using materials that have lower embodied carbon, but successful design solutions are increasingly being shared. Another challenge is availability. Highly recycled steel, sustainably sourced CLT, low carbon concrete etc are all in high demand with limited supply. Manufacturing capacity and output of these materials will need to expand if net zero carbon targets are to be achieved.
In the UKGBC’s study, the use of concrete and steel contributed a total 49% (460 out of 930kgCO2e/m²) of upfront (ie embodied) carbon in the baseline office building design[10]. Using a full structural timber frame with CLT floors and glulam bracing (all of which are recyclable at the end of their life – albeit with some technical and logistical impediments) will produce significant embodied carbon savings. Under the UKBGC’s stretch design, all steelwork was removed (other than connection plates and fixings) but the structure was still founded on concrete pile caps and piles, with a suspended concrete slab forming the ground floor. Therefore not all of the potential 460kgCO2e/m² of upfront carbon savings (that would have come from completely removing steel and concrete) were realised in this scenario. Instead, there was a 39% total upfront carbon reduction compared to the baseline scenario.
Granted, using a full structural timber frame does mean that some concessions have to be made. Additional structural columns and an increase in column size due to the lower strength and stiffness of glulam does result in a loss of floor space. Furthermore, because large services cannot be passed through the timber structure, either the ceiling build ups have to be increased or a change in servicing strategy is required. Ultimately, this increased the floor-to-floor height from 3.6m in the baseline design to 3.85m in the intermediate and stretch designs, resulting in one less floor (within broadly the same volume as the baseline design). This would impact the building’s final value.
Conclusion
The progressive interim carbon reduction targets provided by bodies such as RIBA, LETI and the UKGBC have helped massively but currently, these targets are not fully aligned and lack standardised methodologies and validation mechanisms. Although the various professional bodies intend to develop and refine these carbon targets, it would be far clearer if there were a mutually-agreed, single benchmark for the construction industry to aim for. Regardless, these benchmarks provide a useful first step whilst further refinement and collaboration on targets is being undertaken. They are necessary to help the industry stay on course to reach the Government's overarching goal of being net zero by 2050. Although difficult to achieve, on an operational basis net zero carbon is already possible. The bigger challenge really lies with embodied carbon.
Although it ultimately proved difficult to iterate the baseline designs in an effort to reach the intermediate (2025) and stretch (2030) carbon targets, some of the targets in the UKGBC’s feasibility study were arguably not met due to limitations of the study. For example, having to adhere to project briefs and limitations of the building design with regards to orientation and massing. Allowing flexibility to deviate more from the project brief may improve project viability and help achieve (or at least move closer towards) the net zero carbon targets.
The intermediate (2025) carbon targets are just about feasible today but achieving them does result in a capital cost uplift. In the UKGBC’s residential block scenario, both the 2025 embodied and operational carbon targets were met but resulted in a construction cost uplift of 3.5%. In the UKGBC’s office scenario, despite a cost uplift of 6.2% (compared to the baseline design) the embodied and operational carbon figures achieved under the 2025 scenario were still 25.8% and 28.9% (respectively) above the adopted performance targets. Reaching these intermediate carbon targets would require utilising some of the key design changes from the stretch scenario, resulting in an even greater cost premium and further reductions in floor area and sellable NIA.
The more demanding 2030 targets, however, may be considered unfeasible today given the higher cost premium. We will need to see a transformation of the market and supply chain over the next few years in order for these targets to become feasible. Delivering net zero buildings at scale will require major changes to the current design and delivery process. Greater collaboration and stakeholder buy-in across the value chain will also be needed to reach our goal of net zero carbon buildings.
Despite the potentially higher capital costs needed to achieve these targets, we must not forget the range of whole life benefits that low/zero carbon buildings bring:
- Higher values and rental premiums (6-11%)[11] due to environmental attributes
- Lower tenancy void periods[12]
- High demand from tenants due to strong links to health and wellbeing benefits and reputational benefits
- Lower energy/operational costs due to higher energy efficiency
- Lower maintenance and replacement costs due to designing for durability
- Lower demolition costs due to designing for circularity
- Less need for carbon offsetting
When factored in using a whole life cost analysis, these attributes could potentially balance out any increased capital/ construction costs.
Finally, the Government, which is responsible for roughly 40% of construction spending a year[13], can help accelerate demand for low/zero carbon buildings by restructuring their procurement process to encourage greater use of low carbon materials. Equally, all public sector projects could adopt carbon-intensity targets and mandate whole-life carbon assessments. Taking such steps could help propel the use of low carbon materials from niche to mainstream.
[1] https://www.ukgbc.org/ukgbc-wo...
[2] UK Green Building Council (UKGBC)’s Net Zero Carbon Buildings: A framework definition and Energy Performance Targets for Offices
[3] London Energy Transformation Initiative (LETI)’s Climate Emergency Design Guide
[4] Royal Institute of British Architects (RIBA)’s 2030 Climate Challenge
[5] RICS (2017), Whole life carbon assessment for the built environment: https://www.rics.org/uk/uphold...
[6] https://www.architecture.com/a...
[7] https://www.ukgbc.org/ukgbc-wo...
[8] Stockholm Environment Institute (2018), Low-emission steel production – decarbonising heavy industry: https://www.sei.org/perspectiv...
[9] International Energy Agency (2018), Technology Roadmap: Low-Carbon Transition in the Cement Industry: https://www.iea.org/reports/te...
[10] https://www.ukgbc.org/ukgbc-wo...
[11] JLL (2020), The Impact of Sustainability on Value: https://www.jll.co.uk/en/trend...
[12] JLL (2020), The Impact of Sustainability on Value: https://www.jll.co.uk/en/trend...
[13] Designing Buildings Wiki, ‘Government Construction Strategy 2016 2020’, https://www.designingbuildings...